Nitty gritty methodology, new construction.
OK, we have fiddle faddled around with theory long enough. If you’ve read the whole blog, you realize that there are definite, if not overwhelming advantages to having a well insulated house. By well insulated, we do not mean the paltry “rated” r-17 or r-19 as proposed by conventional builders. That’s as high as they will want to go, since that’s all you can normally get with a 2”x6” stud wall with fiberglass insulation. And they will say, “HEY, that’s pretty good. It’s already 50% better than standard construction.”
True, at least on paper. There are at least three big flaws in their thinking:
1. The actual, measured r-values of fiberglass in very cold conditions (when it really matters) are often half of the rated r-values.
2. Approximately 20% of the wall is wood rather than fiberglass in conventional stud construction. Wood had an r-value of approximately r-1 per inch. So our 2x6 (which is actually 5 ½ inches on a good day, really only has r-5.5. Thermally speaking, r-5 is a hole in the wall.
3. It takes a very well trained and conscientious crew to install fiberglass without gaps, or stuffing, etc. Without a perfect installation, performance suffers considerably.
So, let’s do something different than the herd. If you are going to build a new house, you have a variety of methods available to attain the pinnacle of heating and cooling efficiency, along with unparalleled comfort. I will outline the basics and show you where to get oodles of detailed information.
Obviously, we need a lot of insulation, and a lot of space in the wall to put that insulation. But in addition to that, there are a number of places in a conventionally built house that have little or no insulation, which is dumb. Next time I will show you those weak spots and how to remedy them.
Wall systems:
1. Double wall framing. You literally build two walls, and inner and an outer. Since the inner and outer wall framing don’t touch, that provides a thermal break to dramatically cut heat loss through the wood. This is normally done with a pair of studs 24 inches apart, or “on center” as it is know in the trade. Using two studs every 24 inches is about as strong as using one stud every 12 inches. “Normal” framing uses one stud every 16 inches. So if you live in a place that can get hurricanes, or tornadoes or earthquakes (you know, like all of North America) you will get a stronger house this way as a bonus.
Some framers build the outer wall, then build the inner wall and then build plywood boxes for all the door and window rough openings. Others build both the inner and outer together. This guarantees that all the rough openings will be in the same place and match perfectly, but it also makes the wall twice as heavy to tilt up.
Another advantage of the double wall system is you can have as much insulation as you want with no further increase in framing cost. You can make the gap between the inside and outside wall as big as you want. In my house, I had a 3.5” outer stud, then a 3.5” gap, then a 3.5” inner stud, for a grand total of 10.5” of insulation space. With blown in cellulose that gives you approximately:
r 3.8/in x 10.5in = r39.9
Let’s call it r-40. We will lose some of that since we do have some wood in the wall, and some windows and doors, but we will still end up well above the magic r-30.
2. The 2x6 method. As I have ranted about earlier, just jumping from 2x4 to 2x6 is really not a big improvement, especially when using fiberglass. But there are ways to push this up to very high levels of insulating power.
First, don’t use fiberglass. I don’t know who these people are paying to get their lab results, but this is a big scam. Only in the laboratory will r-13 fiberglass actually give you r-13. In real world conditions, like really cold weather, or really damp weather, or cold damp weather, or a construction crew that doesn’t perfectly install 14.5” batts into perfectly spaced stud bays that are exactly 14.5” wide, with studs that aren’t warped or twisted at all, this stuff typically loses 30-50% of its advertised r-factor. DON’T USE FIBERGLASS.
Blown in cellulose can produce twice the real world insulating power and it’s not hard to get it installed right. So that would give us an actual r-21 for the stud bay itself. To get to r-30, we strap on some foam insulation inside and out. Blue high density Styrofoam insulation is r-5 per inch. If we strap 2” on the outside and 2” on the inside, that gives us:
r-21 + r-10 + r-10 = r-41
So you can literally glue the foam to the studs, and then install your drywall over that using 3” drywall screws. Same thing with the siding on the outside, just use longer fasteners.
Some folks don’t like using the longer fasteners, so there are other legitimate methods as well. You can nail 2x2’s over the 2x6’s, going the other direction. 2x6’s vertical, 2x2’s horizontal. This is called furring out, or strapping out. Installing the 2x2’s at 90 degrees to the studs prevents the wood from all lining up and causing thermal bridges again. This also gives you something solid to nail your electrical boxes to. Plus, you don’t have to use the extra long fasteners, just your normal method of attaching the drywall, screws, nail gun, whatever. You can also use the 2x2 strapping on the outside for easier installation of the siding.
3. 2x6 plus superfoam. There are some spray-in foam products and some ridid foam products that have insulation values of almost r-7 per inch. I hear you ooohing and aaaahing out there. Yes, this is freaking amazing stuff. By comparison, real world r-values for fiberglass (what they want to install in your house) is probably r-2 per inch. So, in theory, we could get:
r-7/in x 5.5” = r-38.5
We still lose a fair amount because every single stud constitutes a thermal bridge that will (relatively speaking) hemorrhage heat out of your house in the winter. We could solve that by putting just a one inch layer of polyisocyanurate foam board over the studs and then drywalling as per normal. This works like gangbusters, but the high tech foam is expensive, both the spray-in kind, and the rigid board kind. But your framing crew will hum along like always which saves time and money, because they have done this framing system a million times. This might be a way to convince a hesitant contractor to give a reasonable bid, since it minimizes the use of “weird” framing.
4. ICF, which stands for Insulated Concrete Form. Pouring concrete vertically (walls, not floors) means building a very strong form, pouring the concrete, and then removing the forms after it gets hard. The forms tend to be expensive and tend to wear out fast. So, some bright fellow thought, “Hey, let’s leave the forms on, and insulate at the same time.” The ICF was born. While these houses are generally not inexpensive, they don’t have to be ridiculously expensive either.
The technology has penetrated the building trades enough that your general contractor won’t think you’re a fruit loop for specifying this method. And because you don’t have to remove the forms, you save labor which offsets some of the cost of the proprietary form system. You will also end up with a tremendously strong house that is fairly resistant to the wind loads that come along with tornados and hurricanes.
There are some downfalls. Concrete is expensive which pushes the cost up. Portland cement (the “active” ingredient in concrete) also requires a lot of energy to manufacture. This is known as embodied energy. Since the whole goal of the exercise is to conserve energy, this is a big minus. This might be offset by the superior durability but the jury is still out on that one.
The promoters of this system sometimes claim performance equal to a conventional r-40 house. Notice how they do not claim r-40 in their product. I think they do this little sleight of hand by using a fiberglass r-40 house for comparison. This is wild speculation on my part. I looked at many web sites promoting ICF’s in one way or another. The vast majority merely stated that they were energy efficient and/or environmentally friendly. Until you show me the data, this is meaningless drivel.
Here’s one that actually names a figure (a whopping r-24), but then boldly state that they perform like houses with much higher levels of insulation. This is actually true if you are comparing it to a conventional house with a just lot of fiberglass stuffed in there, but no additional superinsulation features. But compared with a properly superinsulated house, this is nothing special. We will address the issues of thermal mass in a later column.
http://www.logixicf.com/client/LogixICF/FAQ.nsf/Web/A4E17694897D3F7485256D4C004FDC6A?OpenDocument
So, certainly, ICF’s represent a huge improvement over conventional practice. But I would like to see them get real world r-values over r-30 before I plunk down my money.
So those are the basic methods of building a new house with gobs of insulation in the walls. If that’s all we did, we would make a big difference in energy use, but we would miss some opportunities to finish the job. Next time, we will look at (and eliminate) the thermal weak spots in a conventionally framed house.
If you’re thinking of building any time soon, you need to start a library. Here’s an older book on the subject that has stood the test of time:
http://www.thatnewpublishingcompany.com/super/
Doing a google search for superinsulation will also get you a jillion hits if you’re looking for something useful to do rather than watch bad tv.
Actual progress on the farm house: shot three squirrels with three shots. Squirrel hunters are possibly the primary reason we beat the British in the revolutionary war. Squirrel is not bad eating and has more fat than rabbit. So, back in the day, lots of rural folk shot squirrel to embellish the soup pot and reduce crop losses. But squirrels are tiny, and jumpy. If you can shoot squirrels, preferably in the head so you don't mess up the meat, then shooting a British chap in a bright red suit is a piece of cake. The marksmanship and the weaponry of the Brittish definitely did not compare well with the hunters of the colonies.
I have not heard the little beasties crawling around doing destructive things in my walls. No deer yet, bambi has been very shy since hunting season opened.
Finest regards,
troy and christina
The process of converting a lovely old farmhouse into an efficient cheap-to-heat comfortable home and the life we lead while doing it.
Wednesday, November 22, 2006
Wednesday, November 01, 2006
Comfort levels and "temperature"
Most thermostats for heating and cooling systems measure air temperature. Mostly, they do it that way because its easy and cheap. It has it's limitations however. That's because humans perceive temperature by three different mechanisms, one of which is air temperature.
This is a worthwhile topic because superinsulated house design with intelligent choice of heating systems addresses all three mechanisms. Folks who build conventional houses are generally ignorant of this phenomenon, and their finished product may turn out pretty good by accident, or not so good.
Intuitively, many people are aware of this on some level. Perhaps you have experienced a house where the thermostat/thermometer said you should be comfortable, yet you feel cold. Another common example is a cool, sunny, still day (outside), yet you feel comfortable walking around in short sleeves.
Humans perceive temperature in three ways:
1. Air temperature
2. The temperature of the objects that they are touching (eg sitting on a nice cold toilet seat in January)
3. The temperature of the objects in the room that they are NOT touching.
So let's unpack this a little bit. These three mechanisms of perceiving temperature are really just another way of describing the physics of heat transfer. If we state the three mechanisms like the physicists do, we get this:
1. Convection
2. Conduction
3. Radiation
1. Convection is heat transfer from object 1 (like your furnace) to object 2 (that would be you) by means of an intermediate heat transfer fluid (in this case, air). The furnace heats the air, and the air heats you. You don't have to physically touch the furnace to feel its effects.
2. Conduction is direct transfer of thermal energy from object 1 to object 2 and requires physical contact, like your cold toilet seat in January.
3. Radiation heat transfer is where a hot object radiates heat in all directions as infrared radiation. Common examples would be standing in front of a campfire or woodstove. You can feel the heat even though you are not touching the fire (hopefully) and it feels great despite the fact that there may be cold air all around you. The air is not heated as an intermediary, the heat is transferred very efficiently and directly to you. It is just in the nature of the universe that heat radiates from the hotter object to the colder object.
To flesh this out a bit, we'll do a thought experiment.
Imagine yourself in a room that has an air temperature of 70F. That's considered "warm" or comfortable, all things being equal. But all things are never equal. Now imagine that it's 0F outside and this room has a lot of old single pane inefficient windows along one wall. Even though it is not windy, and the room is not drafy, the room feels cold. You (the hot object) are radiating heat like mad, and those single pane windows act like an infinite heat sink. You will never warm the windows up, they will just keep sucking the heat right out of you.
Now imagine this room, and imagine that it's blustery and howling windy outside. In addition to the massive radiant heat loss, you also have a bad draft. Even though the measured air temperature is still our "toasty" 70F, this room will be uncomfortably cold, and it will be virtually impossible to sit on a couch for any length of time without a blanket. To attain comfort in this room may require air temps in the 80's, if it can be attained at all. If you have your feet in a tub of ice cold water (very high conductive heat losses), you can't make the air temperature hot enough to compensate. As you can readily see, air temperature is only part of the story.
Finally, imagine that our room now has a "normal" (ie modest) window instead of a whole bank of windows. The window is double or triple glazed (two or three layers) and is argon filled (to lower convective heat loss) and a Low-E coating (to reduce emissivity, which reduces radiant heat losses, sometimes known as a heat mirror). Also, let us imagine that the exterior wall is insulated to a true r-30, rather than an effective r-8 in our first room. Further, let us imagine that we have radiant heating in the floor rather than conventional forced air heating.
This does a number of things. The reduced area of glass dramatically reduces radiant heat loss, even if we had the old inefficient single pane window. Keep in mind that even a "good" window still has only r-5 to r-7 at the most. Lots of glass is a bad idea. We try to minimize the losses through the glass that we do have with modern window construction. This does reduce radiant loss and convective losses.
The airtight house construction (which is an integral part of superinsulation techniques) eliminates air infiltration from outdoors, regardless if it is windy or still. The warm radiant floor heats the objects in the room including you and the furniture and walls, by direct radiant heat transfer. Since the objects in the room are no longer cold, your radiant heat loss goes effectively to zero. In fact, you are now the recipient of radiant heat gain. And since your feet are probably on the floor, you also benefit from conductive heat gain, rather than heat loss to a cold floor. Lot's of folks have the idea that heat rises. That's not really true. Hot air rises. Pure heat (in the form of infrared radiation) radiates in all directions, eliminating thermal stratification (hot ceiling/cold floor).
So now that the floor feels warm, and the windows don't feel cold, and the furniture isn't cold, and you don't have a cold draft, you may be totally comfortable and warm with an air temperature of 63F or less. Purveyors of radiant heating systems often claim 20-40% better efficiency than forced air heating. Radiant heating is a more efficient way of giving you good perceived comfort without resorting to high air temperatures.
Congratulations, you now know more about perceived temperature and comfort issues than >95% of all the contractors out there.
Finest regards,
troy
This is a worthwhile topic because superinsulated house design with intelligent choice of heating systems addresses all three mechanisms. Folks who build conventional houses are generally ignorant of this phenomenon, and their finished product may turn out pretty good by accident, or not so good.
Intuitively, many people are aware of this on some level. Perhaps you have experienced a house where the thermostat/thermometer said you should be comfortable, yet you feel cold. Another common example is a cool, sunny, still day (outside), yet you feel comfortable walking around in short sleeves.
Humans perceive temperature in three ways:
1. Air temperature
2. The temperature of the objects that they are touching (eg sitting on a nice cold toilet seat in January)
3. The temperature of the objects in the room that they are NOT touching.
So let's unpack this a little bit. These three mechanisms of perceiving temperature are really just another way of describing the physics of heat transfer. If we state the three mechanisms like the physicists do, we get this:
1. Convection
2. Conduction
3. Radiation
1. Convection is heat transfer from object 1 (like your furnace) to object 2 (that would be you) by means of an intermediate heat transfer fluid (in this case, air). The furnace heats the air, and the air heats you. You don't have to physically touch the furnace to feel its effects.
2. Conduction is direct transfer of thermal energy from object 1 to object 2 and requires physical contact, like your cold toilet seat in January.
3. Radiation heat transfer is where a hot object radiates heat in all directions as infrared radiation. Common examples would be standing in front of a campfire or woodstove. You can feel the heat even though you are not touching the fire (hopefully) and it feels great despite the fact that there may be cold air all around you. The air is not heated as an intermediary, the heat is transferred very efficiently and directly to you. It is just in the nature of the universe that heat radiates from the hotter object to the colder object.
To flesh this out a bit, we'll do a thought experiment.
Imagine yourself in a room that has an air temperature of 70F. That's considered "warm" or comfortable, all things being equal. But all things are never equal. Now imagine that it's 0F outside and this room has a lot of old single pane inefficient windows along one wall. Even though it is not windy, and the room is not drafy, the room feels cold. You (the hot object) are radiating heat like mad, and those single pane windows act like an infinite heat sink. You will never warm the windows up, they will just keep sucking the heat right out of you.
Now imagine this room, and imagine that it's blustery and howling windy outside. In addition to the massive radiant heat loss, you also have a bad draft. Even though the measured air temperature is still our "toasty" 70F, this room will be uncomfortably cold, and it will be virtually impossible to sit on a couch for any length of time without a blanket. To attain comfort in this room may require air temps in the 80's, if it can be attained at all. If you have your feet in a tub of ice cold water (very high conductive heat losses), you can't make the air temperature hot enough to compensate. As you can readily see, air temperature is only part of the story.
Finally, imagine that our room now has a "normal" (ie modest) window instead of a whole bank of windows. The window is double or triple glazed (two or three layers) and is argon filled (to lower convective heat loss) and a Low-E coating (to reduce emissivity, which reduces radiant heat losses, sometimes known as a heat mirror). Also, let us imagine that the exterior wall is insulated to a true r-30, rather than an effective r-8 in our first room. Further, let us imagine that we have radiant heating in the floor rather than conventional forced air heating.
This does a number of things. The reduced area of glass dramatically reduces radiant heat loss, even if we had the old inefficient single pane window. Keep in mind that even a "good" window still has only r-5 to r-7 at the most. Lots of glass is a bad idea. We try to minimize the losses through the glass that we do have with modern window construction. This does reduce radiant loss and convective losses.
The airtight house construction (which is an integral part of superinsulation techniques) eliminates air infiltration from outdoors, regardless if it is windy or still. The warm radiant floor heats the objects in the room including you and the furniture and walls, by direct radiant heat transfer. Since the objects in the room are no longer cold, your radiant heat loss goes effectively to zero. In fact, you are now the recipient of radiant heat gain. And since your feet are probably on the floor, you also benefit from conductive heat gain, rather than heat loss to a cold floor. Lot's of folks have the idea that heat rises. That's not really true. Hot air rises. Pure heat (in the form of infrared radiation) radiates in all directions, eliminating thermal stratification (hot ceiling/cold floor).
So now that the floor feels warm, and the windows don't feel cold, and the furniture isn't cold, and you don't have a cold draft, you may be totally comfortable and warm with an air temperature of 63F or less. Purveyors of radiant heating systems often claim 20-40% better efficiency than forced air heating. Radiant heating is a more efficient way of giving you good perceived comfort without resorting to high air temperatures.
Congratulations, you now know more about perceived temperature and comfort issues than >95% of all the contractors out there.
Finest regards,
troy
Monday, October 23, 2006
A brief look at the economics of superinsulation.
First, let me emphasize that my desire to live in a super energy efficient house is not motivated by saving money. Rather, I want a house like that because I think God has commanded me to be a good steward of all of creation, including the energy to heat my house. Sometimes, obedience to God’s will brings immediate blessings, sometimes it brings burdens or even persecution. But regardless of the response of the world, obedience brings its own joy.
In this case however, I think we can have our cake and eat it too.
It is often surprising to people how little it costs for framing and insulation. One hears various numbers, but it is commonly quoted that the cost for labor and materials to frame a new house constitutes about 8-10% of the total cost. (ref: http://www.pierceconstruct.com/trusses.html) Insulation can be perhaps another 5-8% depending.
So, if you pay somebody to build you a new conventional house, and that new house cost $100,000, the framing and insulation would account for approximately 13-18,000 of the total cost. If we change the design of the house to accommodate very high levels of insulation, the framing and insulation cost will typically increase by 50 to 100%. How does that affect your total cost and mortgage payment?
If we assume worst case scenario costs for the super insulated construction, we end up with a house that cost $118,000, an additional $18,000. Not so fast though. At very high levels of insulation, you will need a much smaller furnace, less ductwork (or no ductwork-gasp!) and may get along very nicely using a big water heater for a “furnace”. If that is true, we can recoup $2-4,000 on the furnace. But let’s continue the worst case scenario analysis and assume we don’t save a penny on the furnace.
The mortgage payments on the conventional house will be:
$702.80 per month
assuming an interest rate of 5.75% on a 20 year amortization. As an aside, 30 year mortgages are as dumb as a box of rocks. Ask me why if you don’t already know.
The mortgage payment on the super insulated house will be:
$828.46 per month
with the same interest rate and amortization. The difference being $125.66 per month. Your actual monthly cash flow should be about the same, if not better in the super insulated house. North of the Mason-Dixon line (i.e., the cold states), heating bills should be ¼ to 1/3 of the regular house, and cooling bills are often trivial to non-existent. If your average monthly winter heating bill in the conventional house is $150 (conservative estimate, could easily be higher), in the superinsulated house, it will be:
0.33 x 150 = $50.00 which saves ~$100 per month.
Below the Mason-Dixon line (the hot humid states) you will save the big money on air conditioning bills.
Either way, the super house more or less pays for itself in reduced energy use even in the short term.
But I am not overly swayed by short term economics. Long term efficiencies are very convincing to me. When we consider the long run, once the mortgage is paid for, all that energy saved is essentially “free money”. Another item that is often ignored in these discussions is tax liabilities. Let’s assume we save a thousand dollars every year on energy cost. Those are AFTER TAX dollars we are saving. If you have to go out and spend those thousand dollars on natural gas or electricity, you really have to earn $1,200 or $1,400 first. Then you pay your various taxes on those earnings, then you pay your heating bill. So in reality, we are saving much more than $1,000.
We also have not mentioned anything about future energy cost. In my view of the future and energy cost, it will all become more expensive and it will do so at a brisk pace. Let’s look at natural gas prices in the recent past.
(The HTML did not like my graph, so here is a link to a graph:
http://en.wikipedia.org/wiki/Natural_gas_prices
Please note that this other graph uses different units, which doesn't matter. It's those spikes and general rise at the end we are interested in.)
As we observe the graph, a few things are obvious. Residential gas prices are cyclic, depending on the weather. Every minor peak is the winter price, every trough is the summer price. It’s also hard to miss that in the last ten years, costs have escalated rapidly after a long stable stretch. Just to pick out a few facts:
Gas was
$3.94 in Jan of 1981
$5.54 in Jan of 1991
$10.12 in Jan of 2001
and $14.92 in Jan of 2006
If this trend continues, the cost savings in a super insulated house will likely double in less than ten years, and then double again in less than ten years. So in 20 years, after the mortgage is paid off, the cash flow comparison of the two houses would look more like this:
Annual heating and cooling costs for conventional house:
$7,200
Annual heating and cooling costs for superinsulated house:
$2,397
This represents a savings of about $5,000 per year of after tax, inflation adjusted dollars. If we further assume that the house will last another 80 years and that there are no additional increases in energy cost (unlikely), this will represent a total life cycle savings of approximately:
80 x $5,000 = $400,000
Suddenly, we are not talking about just beer and pizza money any more. This could mean the difference between fixed income seniors being able to afford a house, or not. For low and middle income families, this will make the whole heat vs food issue much worse. Or perhaps they will have to choose between heat and their medications. Or heat vs retirement savings. Or heat vs a college fund for their kids. Or heat vs church giving. Do you really want to be forced to choose?
I could use the techniques used by the slippery insurance/investment industry to make this look wildly “over the top” superior to conventional housing. Rather than just computing everything in today’s dollars and ignoring inflation and interest, we could take that money that we save on energy costs and put that in a nice moderate growth fund and end up with some silly big number like $10,000,000 after 80 years.
But that is speculative, which is really a euphemism for gambling. If you want to invest the money, I’m fine with that. You will probably do very well. But the real point is that in real dollars and real buying power, without any compound interest smoke and mirrors, the superinsulated house beats the conventional house with a big stick, repeatedly. Wouldn’t you like to pass that on to your kids?
When cast in these terms, we suddenly see why this is a stewardship issue. We are all given stewardship over a limited amount of resources. Those who use the resources wisely will end up having many more options in how they use those resources.
There are other issues that can sway the balance in favor of superinsulation. If you can do some or all of your own work, the economics becomes overwhelmingly favorable to the superinsulated house. These houses are almost universally more comfortable to live in. Cold corners, cold floors, and cold rooms are a thing of the past. At high levels of insulation, the thermostat setting has less and less influence over how much you save by turning it down. It’s the law of diminishing returns. As a consequence, you can now keep it at 70F all winter if you like and walk around in shorts and a tee shirt without wasting abhorrent amounts of energy and money.
This is not theoretical. When I finally got my house in Ontario Canada closed in and insulated, we were definitely in winter. I was working on finishing the interior, drywall and whatnot. Every single day that was sunny, the furnace did not run during the day and it would be toasty warm, even on bitterly cold days in January. Visitors were often amazed to find me working in just shorts, or maybe shorts and a tee shirt, despite the winter weather. Most had never experienced that luxury due to the cost of fuel.
One gentleman in particular was doubtful that he could even get his house that warm, even running the woodstove full blast all day long. He lived in an old farm house without much/any insulation. He reported that they burned about 14 cords of wood every winter, which is an enormous pile of work and expense. It was still cold. His house is the antithesis to mine.
Of course, if you work at it, you can find some circumstance where you don’t actually save any money. Perhaps the remodeling to install that much insulation is fairly expensive. Perhaps you end up with a general contractor who is unfamiliar with the framing techniques to achieve these r-values. The work goes slower, the labor costs go up, the materials cost from waste goes up, and you end up way over budget. Perhaps the starting house is reasonably well insulated to start with, giving less room for improvement and savings.
Perhaps you build or remodel and end up with your dream superinsulated house, only to discover that you have to move in two years because of a job transfer. Don’t despair yet. The resale value on a superinsulated house with a demonstrated track record of low fuel bills will definitely bring a higher price. But whether you recoup all of your additional investment or not depends on 27 other factors that we have little or no control over.
In the long run, none of the economic issues really matters because this is not about the money. Saving money in the long run is just a nice byproduct. The goal is to be frugal with the energy we are given out of respect for God and respect for our kids and grandkids. I would do it even if I “lost” money.
Finest regards,
troy and christina
First, let me emphasize that my desire to live in a super energy efficient house is not motivated by saving money. Rather, I want a house like that because I think God has commanded me to be a good steward of all of creation, including the energy to heat my house. Sometimes, obedience to God’s will brings immediate blessings, sometimes it brings burdens or even persecution. But regardless of the response of the world, obedience brings its own joy.
In this case however, I think we can have our cake and eat it too.
It is often surprising to people how little it costs for framing and insulation. One hears various numbers, but it is commonly quoted that the cost for labor and materials to frame a new house constitutes about 8-10% of the total cost. (ref: http://www.pierceconstruct.com/trusses.html) Insulation can be perhaps another 5-8% depending.
So, if you pay somebody to build you a new conventional house, and that new house cost $100,000, the framing and insulation would account for approximately 13-18,000 of the total cost. If we change the design of the house to accommodate very high levels of insulation, the framing and insulation cost will typically increase by 50 to 100%. How does that affect your total cost and mortgage payment?
If we assume worst case scenario costs for the super insulated construction, we end up with a house that cost $118,000, an additional $18,000. Not so fast though. At very high levels of insulation, you will need a much smaller furnace, less ductwork (or no ductwork-gasp!) and may get along very nicely using a big water heater for a “furnace”. If that is true, we can recoup $2-4,000 on the furnace. But let’s continue the worst case scenario analysis and assume we don’t save a penny on the furnace.
The mortgage payments on the conventional house will be:
$702.80 per month
assuming an interest rate of 5.75% on a 20 year amortization. As an aside, 30 year mortgages are as dumb as a box of rocks. Ask me why if you don’t already know.
The mortgage payment on the super insulated house will be:
$828.46 per month
with the same interest rate and amortization. The difference being $125.66 per month. Your actual monthly cash flow should be about the same, if not better in the super insulated house. North of the Mason-Dixon line (i.e., the cold states), heating bills should be ¼ to 1/3 of the regular house, and cooling bills are often trivial to non-existent. If your average monthly winter heating bill in the conventional house is $150 (conservative estimate, could easily be higher), in the superinsulated house, it will be:
0.33 x 150 = $50.00 which saves ~$100 per month.
Below the Mason-Dixon line (the hot humid states) you will save the big money on air conditioning bills.
Either way, the super house more or less pays for itself in reduced energy use even in the short term.
But I am not overly swayed by short term economics. Long term efficiencies are very convincing to me. When we consider the long run, once the mortgage is paid for, all that energy saved is essentially “free money”. Another item that is often ignored in these discussions is tax liabilities. Let’s assume we save a thousand dollars every year on energy cost. Those are AFTER TAX dollars we are saving. If you have to go out and spend those thousand dollars on natural gas or electricity, you really have to earn $1,200 or $1,400 first. Then you pay your various taxes on those earnings, then you pay your heating bill. So in reality, we are saving much more than $1,000.
We also have not mentioned anything about future energy cost. In my view of the future and energy cost, it will all become more expensive and it will do so at a brisk pace. Let’s look at natural gas prices in the recent past.
(The HTML did not like my graph, so here is a link to a graph:
http://en.wikipedia.org/wiki/Natural_gas_prices
Please note that this other graph uses different units, which doesn't matter. It's those spikes and general rise at the end we are interested in.)
As we observe the graph, a few things are obvious. Residential gas prices are cyclic, depending on the weather. Every minor peak is the winter price, every trough is the summer price. It’s also hard to miss that in the last ten years, costs have escalated rapidly after a long stable stretch. Just to pick out a few facts:
Gas was
$3.94 in Jan of 1981
$5.54 in Jan of 1991
$10.12 in Jan of 2001
and $14.92 in Jan of 2006
If this trend continues, the cost savings in a super insulated house will likely double in less than ten years, and then double again in less than ten years. So in 20 years, after the mortgage is paid off, the cash flow comparison of the two houses would look more like this:
Annual heating and cooling costs for conventional house:
$7,200
Annual heating and cooling costs for superinsulated house:
$2,397
This represents a savings of about $5,000 per year of after tax, inflation adjusted dollars. If we further assume that the house will last another 80 years and that there are no additional increases in energy cost (unlikely), this will represent a total life cycle savings of approximately:
80 x $5,000 = $400,000
Suddenly, we are not talking about just beer and pizza money any more. This could mean the difference between fixed income seniors being able to afford a house, or not. For low and middle income families, this will make the whole heat vs food issue much worse. Or perhaps they will have to choose between heat and their medications. Or heat vs retirement savings. Or heat vs a college fund for their kids. Or heat vs church giving. Do you really want to be forced to choose?
I could use the techniques used by the slippery insurance/investment industry to make this look wildly “over the top” superior to conventional housing. Rather than just computing everything in today’s dollars and ignoring inflation and interest, we could take that money that we save on energy costs and put that in a nice moderate growth fund and end up with some silly big number like $10,000,000 after 80 years.
But that is speculative, which is really a euphemism for gambling. If you want to invest the money, I’m fine with that. You will probably do very well. But the real point is that in real dollars and real buying power, without any compound interest smoke and mirrors, the superinsulated house beats the conventional house with a big stick, repeatedly. Wouldn’t you like to pass that on to your kids?
When cast in these terms, we suddenly see why this is a stewardship issue. We are all given stewardship over a limited amount of resources. Those who use the resources wisely will end up having many more options in how they use those resources.
There are other issues that can sway the balance in favor of superinsulation. If you can do some or all of your own work, the economics becomes overwhelmingly favorable to the superinsulated house. These houses are almost universally more comfortable to live in. Cold corners, cold floors, and cold rooms are a thing of the past. At high levels of insulation, the thermostat setting has less and less influence over how much you save by turning it down. It’s the law of diminishing returns. As a consequence, you can now keep it at 70F all winter if you like and walk around in shorts and a tee shirt without wasting abhorrent amounts of energy and money.
This is not theoretical. When I finally got my house in Ontario Canada closed in and insulated, we were definitely in winter. I was working on finishing the interior, drywall and whatnot. Every single day that was sunny, the furnace did not run during the day and it would be toasty warm, even on bitterly cold days in January. Visitors were often amazed to find me working in just shorts, or maybe shorts and a tee shirt, despite the winter weather. Most had never experienced that luxury due to the cost of fuel.
One gentleman in particular was doubtful that he could even get his house that warm, even running the woodstove full blast all day long. He lived in an old farm house without much/any insulation. He reported that they burned about 14 cords of wood every winter, which is an enormous pile of work and expense. It was still cold. His house is the antithesis to mine.
Of course, if you work at it, you can find some circumstance where you don’t actually save any money. Perhaps the remodeling to install that much insulation is fairly expensive. Perhaps you end up with a general contractor who is unfamiliar with the framing techniques to achieve these r-values. The work goes slower, the labor costs go up, the materials cost from waste goes up, and you end up way over budget. Perhaps the starting house is reasonably well insulated to start with, giving less room for improvement and savings.
Perhaps you build or remodel and end up with your dream superinsulated house, only to discover that you have to move in two years because of a job transfer. Don’t despair yet. The resale value on a superinsulated house with a demonstrated track record of low fuel bills will definitely bring a higher price. But whether you recoup all of your additional investment or not depends on 27 other factors that we have little or no control over.
In the long run, none of the economic issues really matters because this is not about the money. Saving money in the long run is just a nice byproduct. The goal is to be frugal with the energy we are given out of respect for God and respect for our kids and grandkids. I would do it even if I “lost” money.
Finest regards,
troy and christina
Friday, October 13, 2006
Olympic barrel wrestling...
I am happy to announce that actual progress was made on the farm house. We now have almost fully functional heat, which is a good thing in October. Shortly after moving in, I fired up the boiler to see if it worked at all. The boiler itself came on when the thermostat called for heat, so that was a good sign, but the heat didn’t seem to make it out to the hot water baseboards. So I shut it down and left it, heat not being a critical issue in July.
By October of course, it had moved up many rungs on the list. I was afraid it would take major surgery and big bucks to get it back online, but the fix was pretty easy. The pipes were at least half full of air. This may have been due to neglect, which would have fit right in with the PO’s (previous owner’s) style. Or it could have been a technical difficulty. All boilers have some provision for make-up water. For various reasons like the solubility of air in cold water vs hot water, they all tend to get a bit of air in the system. Ours has some kind of valve for adding water, but either it’s broken, or I don’t understand how it works.
Work-arounds are my specialty. I found a spigot on one of the lines, and two bleeder valves upstairs. I made up a special chunk of garden hose that was female on both ends that allowed me to hook a garden hose up to the spigot and add water to the system that way. After several iterations of filling and bleeding air, the system took off like gangbusters and we now have heat in most rooms.
For reasons that are obscure to me, one of the upstairs bedrooms has no baseboard radiators (they are really convectors, but nobody uses that word which is a pity). Maybe the kids liked it a bit chilly in the winter. It's also the room that's painted electric orange with butterflies and it had a lock on the outside of the door. We may never really know what went on in that room, hopefully.
I invented a new Olympic sport while moving stuff in and out of the basement. Well, maybe it’s not quite Olympic caliber. Perhaps it is more like one of those goofy strongman competition sports. OK, being totally honest, it’s more like a “sport” you would end up seeing on Worlds Funniest Home Videos. By now you should be realizing that I tried a stupid stunt and almost broke my neck in the process. I am happy to report I was unsuccessful in that respect.
It all started innocently enough. I was moving possessions from the trailer into the basement. I got the idea that, hey, every trip out I could remove some junk/crap that needs throwing away. You know, efficiency and all that. One of the things that had to go was the “wood stove” that was in the basement. By wood stove, I mean the 55 gallon steel drum that had a primitive door and a primitive flue pipe bolted on. Primitive is really a kindness when describing this contraption.
It was still about 1/3 full of ashes, and the remaining space crammed with beer cans, jetsam and insulation scraps. I strapped it to my nice two wheeled dolly and determined to heave it up the stairs myself. I am moderately stout, and it wasn’t that heavy right? So I’m working my way up the stairs slowly and carefully. About 2/3 of the way up, I notice that somehow, every time I jerk it up one more stair, it drops a nice little pile of ashes on the stair.
I was pretty sure I had strapped the door shut, so I was puzzled by this. While carefully balancing the monster, I craned my head around to get a better look. To my horror, I realized that those corrosive ashes had destroyed about half of the joint where the bottom attaches to the drum and could fail catastrophically with one more good jolt, dumping ashes everywhere.
What to do, what to do? I decided that if I very gently raised it up the last three stairs, it would hold. And since I’m so athletic and coordinated and lucky, this should be no problem. In hindsight, I realized that this assumption was like the young innocent girl who decides to find out what that scary noise was down in the basement of a B-class horror flick. "DON’T DO IT!!", you should be yelling about now.
Essentially, I tried to raise it over each stair in slow motion, using exquisite control, avoiding the sudden jolting that would cause the whole precarious mess to fall apart and come crashing down. The first stair went well. The second stair, I hesitated just a fraction of a second, and it slipped back down and hit the stair with a jolt. This surprised me and pulled me off balance. In a tiny fraction of a second several things happened.
1. I discovered that a healthy slug of adrenaline takes 20 years off of a 46 year old male in terms of physical strength and agility.
2. The drum, the dolly and I ended up just a hair’s breadth away from tumbling down the stairs.
3. The base of the drum came off the dolly and hung up on the edge of the stair by the hair of its chiny chin chin.
I was prepared to let the whole thing fly down the stairs to prevent the breaking of my own neck or other major bones, but that turned out to be unnecessary. With heroic effort, I got the drum wiggled back on the base of the dolly, got it tied on tighter and successfully negotiated those last couple of stairs without further excitement. Thankfully, no video cams were about to record my prowess for posterity.
The other progress is that I got the north room in the basement cleaned out. I removed the old pressure tank and the crusty dirty rotten shelves. When they put the new well in, they just abandoned the old galvanized pressure tank and pushed it over to the side, still full of water. It was a heavy pig, and I couldn’t get any of the rusty plugs out, so I ended up drilling a hole and draining the water that way. I also removed all the old nasty shelving from that room. It has been reduced to kindling now. I felt a little bad cutting it up with the circular saw, as they were made out of who-knows how old 1” x 18” boards. Next time you go down to the lumber yard, ask for some twelve foot one by eighteens and see what they say.
The rarity of lumber like that is due to the loss of old growth big trees. Now, most of the 2 x 4’s and whatnot come from managed plots of rapid growth softwood. On the whole, this is a good thing as they are theoretically renewable and sustainable, but nobody wants to wait for the trees to get big enough to make two by twenties, or one by twentyfours. Plywood is a more efficient way to make wide boards these days.
We caught a second rat in the new sump pit. I guess they jump in for a drink because they are thirsty from eating the rat poison and starting to hemorrhage inside. Then they can’t crawl back out and can only tread water for so long. I feel zero sympathy.
After asking my wife if she wanted to remove the soggy carcass this time, we determined that this is man-work, which I don’t really mind. In truth, it was a squirrel, but they are just rats with fluffy tails, and every bit as destructive.
Finest regards, and see you next time.
troy
By October of course, it had moved up many rungs on the list. I was afraid it would take major surgery and big bucks to get it back online, but the fix was pretty easy. The pipes were at least half full of air. This may have been due to neglect, which would have fit right in with the PO’s (previous owner’s) style. Or it could have been a technical difficulty. All boilers have some provision for make-up water. For various reasons like the solubility of air in cold water vs hot water, they all tend to get a bit of air in the system. Ours has some kind of valve for adding water, but either it’s broken, or I don’t understand how it works.
Work-arounds are my specialty. I found a spigot on one of the lines, and two bleeder valves upstairs. I made up a special chunk of garden hose that was female on both ends that allowed me to hook a garden hose up to the spigot and add water to the system that way. After several iterations of filling and bleeding air, the system took off like gangbusters and we now have heat in most rooms.
For reasons that are obscure to me, one of the upstairs bedrooms has no baseboard radiators (they are really convectors, but nobody uses that word which is a pity). Maybe the kids liked it a bit chilly in the winter. It's also the room that's painted electric orange with butterflies and it had a lock on the outside of the door. We may never really know what went on in that room, hopefully.
I invented a new Olympic sport while moving stuff in and out of the basement. Well, maybe it’s not quite Olympic caliber. Perhaps it is more like one of those goofy strongman competition sports. OK, being totally honest, it’s more like a “sport” you would end up seeing on Worlds Funniest Home Videos. By now you should be realizing that I tried a stupid stunt and almost broke my neck in the process. I am happy to report I was unsuccessful in that respect.
It all started innocently enough. I was moving possessions from the trailer into the basement. I got the idea that, hey, every trip out I could remove some junk/crap that needs throwing away. You know, efficiency and all that. One of the things that had to go was the “wood stove” that was in the basement. By wood stove, I mean the 55 gallon steel drum that had a primitive door and a primitive flue pipe bolted on. Primitive is really a kindness when describing this contraption.
It was still about 1/3 full of ashes, and the remaining space crammed with beer cans, jetsam and insulation scraps. I strapped it to my nice two wheeled dolly and determined to heave it up the stairs myself. I am moderately stout, and it wasn’t that heavy right? So I’m working my way up the stairs slowly and carefully. About 2/3 of the way up, I notice that somehow, every time I jerk it up one more stair, it drops a nice little pile of ashes on the stair.
I was pretty sure I had strapped the door shut, so I was puzzled by this. While carefully balancing the monster, I craned my head around to get a better look. To my horror, I realized that those corrosive ashes had destroyed about half of the joint where the bottom attaches to the drum and could fail catastrophically with one more good jolt, dumping ashes everywhere.
What to do, what to do? I decided that if I very gently raised it up the last three stairs, it would hold. And since I’m so athletic and coordinated and lucky, this should be no problem. In hindsight, I realized that this assumption was like the young innocent girl who decides to find out what that scary noise was down in the basement of a B-class horror flick. "DON’T DO IT!!", you should be yelling about now.
Essentially, I tried to raise it over each stair in slow motion, using exquisite control, avoiding the sudden jolting that would cause the whole precarious mess to fall apart and come crashing down. The first stair went well. The second stair, I hesitated just a fraction of a second, and it slipped back down and hit the stair with a jolt. This surprised me and pulled me off balance. In a tiny fraction of a second several things happened.
1. I discovered that a healthy slug of adrenaline takes 20 years off of a 46 year old male in terms of physical strength and agility.
2. The drum, the dolly and I ended up just a hair’s breadth away from tumbling down the stairs.
3. The base of the drum came off the dolly and hung up on the edge of the stair by the hair of its chiny chin chin.
I was prepared to let the whole thing fly down the stairs to prevent the breaking of my own neck or other major bones, but that turned out to be unnecessary. With heroic effort, I got the drum wiggled back on the base of the dolly, got it tied on tighter and successfully negotiated those last couple of stairs without further excitement. Thankfully, no video cams were about to record my prowess for posterity.
The other progress is that I got the north room in the basement cleaned out. I removed the old pressure tank and the crusty dirty rotten shelves. When they put the new well in, they just abandoned the old galvanized pressure tank and pushed it over to the side, still full of water. It was a heavy pig, and I couldn’t get any of the rusty plugs out, so I ended up drilling a hole and draining the water that way. I also removed all the old nasty shelving from that room. It has been reduced to kindling now. I felt a little bad cutting it up with the circular saw, as they were made out of who-knows how old 1” x 18” boards. Next time you go down to the lumber yard, ask for some twelve foot one by eighteens and see what they say.
The rarity of lumber like that is due to the loss of old growth big trees. Now, most of the 2 x 4’s and whatnot come from managed plots of rapid growth softwood. On the whole, this is a good thing as they are theoretically renewable and sustainable, but nobody wants to wait for the trees to get big enough to make two by twenties, or one by twentyfours. Plywood is a more efficient way to make wide boards these days.
We caught a second rat in the new sump pit. I guess they jump in for a drink because they are thirsty from eating the rat poison and starting to hemorrhage inside. Then they can’t crawl back out and can only tread water for so long. I feel zero sympathy.
After asking my wife if she wanted to remove the soggy carcass this time, we determined that this is man-work, which I don’t really mind. In truth, it was a squirrel, but they are just rats with fluffy tails, and every bit as destructive.
Finest regards, and see you next time.
troy
Saturday, September 30, 2006
So you want to heat your house with a candle...here's how.
As a young teen, I became obsessed with solar power and energy efficiency in general. My mom was the librarian at school, and one of the consequences was that I learned how to find information pretty efficiently. So over the years, I have seen or read about practically every trick in the book to heat a house inexpensively and efficiently. Here's a partial list of topics that I researched over the years.
Geodesic domes, These are visually fascinating, "modern", with all the pizzaz of Buckminster Fuller. They also generally leak and finishing all those funny angles is challenging to say the least. Geometrically speaking, domes present 1/3 less surface area per cubic foot of living space enclosed when compared with more conventional square/rectangular/cubic construction. So, all things being equal, they can be energy efficient if you are willing to put up with a few leaks. The average building inspector, along with his whole department, will likely give you trouble. For a brief time I worshipped in a church like this in Caldwell Texas that had the most amazing acoustics for singing.
Monolithic domes, Made out of cement or Gunnite or Shotcrete and reinforced with steel, cool or weird depending on how I feel that day. They can attain very high levels of thermal efficiency because they minimize surface area and they use a kind of foam insulation that may attain r-6 to r-7 per inch, which is twice what you get with fiberglass. As far as real world performance, we are probably talking quadruple the real world insulating power of fiberglass batts in a conventional building. They are also tornado proof. http://www.monolithic.com/ makes for interesting reading.
Tire houses, This is where you stack a tire, ram full of dirt, repeat 2,000 times. Lots of code issues and not that great for insulation. Poor control of moisture. Vast enormous quantities of labor required.
Adobe houses, Omit the tires, just use the dirt. Lousy insulation, but tremendous thermal mass. They work great in sunny, cool, dry or sunny, hot, dry climates, and just about nowhere else. Vast enormous quantity of labor required again.
Bale houses, or strawbale construction, This is where you stack bales of straw rather like Lincoln Logs or giant bricks. Construction itself goes pretty fast and is forgiving of beginners if the design is good. The have pretty good insulation values, which, coming from me is very high praise indeed. Conceptually, I want to take this to its logical extreme and build a house out of big round or big square bales with wall thickness of four feet or more. In many places, straw is considered a waste product that is difficult to dispose of, so this kills two birds with one stone. Some code problems in some places. I am still very tempted...
Log home construction, Romantic, pretty, but real world r-values are not that great and they require considerable special skills to construct. Finding good logs of the needed size is not a trivial task in most places and it's an inefficient way to use the lumber. You could take it apart and build two really efficient houses with that much wood.
Underground houses, These offer almost mythical energy savings, in the sense that real data that proves their claims is as rare as pixies and fairies. Devotees often exhibit religious zeal for this idea. Building a house underground does lower the Delta-T (the difference between inside and outside temperature) but they are still problematic on several levels. You can get equivalent or better energy efficiency in ways that are cheaper and easier to attain. There is a book called "The Fifty Dollar and Up Underground House Book" that is a cult classic. I was almost a hippy back then.
Berm houses, These are sort of underground and are neither fish nor fowl. Ultimately, there are easier and less expensive ways to achieve energy efficiency.
Cobb houses, The English are crazy about cob, it's the English version of adobe more or less, with somewhat better insulating capacity. In both relative and absolute terms, r-values are not that great.
Stackwall, This has had a big revival in the last 20 years or so. You basically buy a load of firewood logs, cut them into pieces all the same length and lay the logs up like bricks to make a wall 18-24 inches thick. r-Values OK but not great. A million cracks to caulk after the logs shrink. They are both pretty and distinctive. Here's a blog by a guy who did a double wall stackwall house that came out very good on the thermal envelope. He's the exception though and it involved massive labor inputs. http://www.daycreek.com/dc/html/journalmenu.htm)
Double Envelope homes, They didn't really save a lot of energy, and if they did, it wasn't because they were double envelope. They were a short lived fad.
Vacuum panel insulation, These are small panels that are almost absolutely airtight and can be installed as insulation They are very much like a thermos bottle. A perfect vacuum doesn't lose any heat by conduction or convection, only radiant losses, which can be controlled. Unfortunately, they are expensive, delicate, and have questionable lifespan. They are not ready for prime time yet.
Active solar heating, tends to be fabulously expensive to provide 100% of the heat for you rhouse unless you cut your heat needs dramatically by superinsulation techniques. Spectacularly unsuccessful in cloudy climates like mine.
Drum wall, Make your south wall essentially all glass. Build a heavy frame to support 55 gal drums of water behind the wall. Build an insulating cover for that south wall that you can open and close so that it doubles as a reflector during the day. These work fairly well if you have a sunny climate and you insulate well. They look funny and it is not a trivial task to build an insulated door for the south wall of your house. Completely unsuitable for remodels.
Trombe Wall solar heating, This is another big bank of south facing glass. But now you build a cement wall about one foot behind it to soak up the heat during the day and release that heat at night when you need it more. It sounds great, but without nighttime insulation over the glass it is terribly inefficient because that hot cement wall radiates and convects that heat very efficiently right back out the window. It's also, ummmm, ugly. Take a big huge window and build a black wall right next to it so you can't see out or in through the "window". It is still widely promoted by the way. If you can insulate the cold glass from the hot thermal mass at night and on cloudy days, then they work fairly well, but then it's not really a Trombe wall either.
Passive solar heating, This can range from extremely successful to wildly impractical and expensive, mostly depending on how much they implement superinsulation techniques.
Ground source heat pumps, They are expensive, complex and have a history of durability problems. Durability has gotten better lately they say. They run on electricity, which often comes from coal or nuclear, so those are not huge enviro winners. 2/3 of all the heat from the original fuel gets wasted at the power plant before it ever arrives at your house, so system wide efficiency suddenly doesn't look so great. If you absolutely have to heat with electricity, this is how you should do it. You need a big lot and the backhoe will dig huge trenches everywhere. Superinsulation techniques would allow you to cut the size of the unit by half or more.
Air to air heat pumps, These are only efficient in milder climates. At temps below freezing, they become very inefficient because they have to use electric resistance heat to prevent frost build up. They are also expensive and complex to maintain, and run on electricity.
Ground water heat pumps, Also expensive, complex and requires at least two wells on the property, often against zoning regs to pump water back into the aquifer.
Outdoor wood furnaces, These have hideously poor efficiency, often less than 25%. The manufacturers often imply good efficiency, but you will universally find that they are short on indepent test data. They virtually all smoke (aka pollution) when operated as suggested in the ads. This is deforestation and pollution right in your own back yard.
Superinsulation. This is the best, period. I'm not biased or anything. Really.
So that's a thumbnail sketch of what is available, what works and what doesn't. I will support my wild claims for superinsulation in subsequent columns.
As far as actual progress on the actual house, nothing. Still fixing up the city house. Got about half of my cogenerator transfer switch unwired from the regular breaker box and will finish that tonight.
Finest regards,
troy
Geodesic domes, These are visually fascinating, "modern", with all the pizzaz of Buckminster Fuller. They also generally leak and finishing all those funny angles is challenging to say the least. Geometrically speaking, domes present 1/3 less surface area per cubic foot of living space enclosed when compared with more conventional square/rectangular/cubic construction. So, all things being equal, they can be energy efficient if you are willing to put up with a few leaks. The average building inspector, along with his whole department, will likely give you trouble. For a brief time I worshipped in a church like this in Caldwell Texas that had the most amazing acoustics for singing.
Monolithic domes, Made out of cement or Gunnite or Shotcrete and reinforced with steel, cool or weird depending on how I feel that day. They can attain very high levels of thermal efficiency because they minimize surface area and they use a kind of foam insulation that may attain r-6 to r-7 per inch, which is twice what you get with fiberglass. As far as real world performance, we are probably talking quadruple the real world insulating power of fiberglass batts in a conventional building. They are also tornado proof. http://www.monolithic.com/ makes for interesting reading.
Tire houses, This is where you stack a tire, ram full of dirt, repeat 2,000 times. Lots of code issues and not that great for insulation. Poor control of moisture. Vast enormous quantities of labor required.
Adobe houses, Omit the tires, just use the dirt. Lousy insulation, but tremendous thermal mass. They work great in sunny, cool, dry or sunny, hot, dry climates, and just about nowhere else. Vast enormous quantity of labor required again.
Bale houses, or strawbale construction, This is where you stack bales of straw rather like Lincoln Logs or giant bricks. Construction itself goes pretty fast and is forgiving of beginners if the design is good. The have pretty good insulation values, which, coming from me is very high praise indeed. Conceptually, I want to take this to its logical extreme and build a house out of big round or big square bales with wall thickness of four feet or more. In many places, straw is considered a waste product that is difficult to dispose of, so this kills two birds with one stone. Some code problems in some places. I am still very tempted...
Log home construction, Romantic, pretty, but real world r-values are not that great and they require considerable special skills to construct. Finding good logs of the needed size is not a trivial task in most places and it's an inefficient way to use the lumber. You could take it apart and build two really efficient houses with that much wood.
Underground houses, These offer almost mythical energy savings, in the sense that real data that proves their claims is as rare as pixies and fairies. Devotees often exhibit religious zeal for this idea. Building a house underground does lower the Delta-T (the difference between inside and outside temperature) but they are still problematic on several levels. You can get equivalent or better energy efficiency in ways that are cheaper and easier to attain. There is a book called "The Fifty Dollar and Up Underground House Book" that is a cult classic. I was almost a hippy back then.
Berm houses, These are sort of underground and are neither fish nor fowl. Ultimately, there are easier and less expensive ways to achieve energy efficiency.
Cobb houses, The English are crazy about cob, it's the English version of adobe more or less, with somewhat better insulating capacity. In both relative and absolute terms, r-values are not that great.
Stackwall, This has had a big revival in the last 20 years or so. You basically buy a load of firewood logs, cut them into pieces all the same length and lay the logs up like bricks to make a wall 18-24 inches thick. r-Values OK but not great. A million cracks to caulk after the logs shrink. They are both pretty and distinctive. Here's a blog by a guy who did a double wall stackwall house that came out very good on the thermal envelope. He's the exception though and it involved massive labor inputs. http://www.daycreek.com/dc/html/journalmenu.htm)
Double Envelope homes, They didn't really save a lot of energy, and if they did, it wasn't because they were double envelope. They were a short lived fad.
Vacuum panel insulation, These are small panels that are almost absolutely airtight and can be installed as insulation They are very much like a thermos bottle. A perfect vacuum doesn't lose any heat by conduction or convection, only radiant losses, which can be controlled. Unfortunately, they are expensive, delicate, and have questionable lifespan. They are not ready for prime time yet.
Active solar heating, tends to be fabulously expensive to provide 100% of the heat for you rhouse unless you cut your heat needs dramatically by superinsulation techniques. Spectacularly unsuccessful in cloudy climates like mine.
Drum wall, Make your south wall essentially all glass. Build a heavy frame to support 55 gal drums of water behind the wall. Build an insulating cover for that south wall that you can open and close so that it doubles as a reflector during the day. These work fairly well if you have a sunny climate and you insulate well. They look funny and it is not a trivial task to build an insulated door for the south wall of your house. Completely unsuitable for remodels.
Trombe Wall solar heating, This is another big bank of south facing glass. But now you build a cement wall about one foot behind it to soak up the heat during the day and release that heat at night when you need it more. It sounds great, but without nighttime insulation over the glass it is terribly inefficient because that hot cement wall radiates and convects that heat very efficiently right back out the window. It's also, ummmm, ugly. Take a big huge window and build a black wall right next to it so you can't see out or in through the "window". It is still widely promoted by the way. If you can insulate the cold glass from the hot thermal mass at night and on cloudy days, then they work fairly well, but then it's not really a Trombe wall either.
Passive solar heating, This can range from extremely successful to wildly impractical and expensive, mostly depending on how much they implement superinsulation techniques.
Ground source heat pumps, They are expensive, complex and have a history of durability problems. Durability has gotten better lately they say. They run on electricity, which often comes from coal or nuclear, so those are not huge enviro winners. 2/3 of all the heat from the original fuel gets wasted at the power plant before it ever arrives at your house, so system wide efficiency suddenly doesn't look so great. If you absolutely have to heat with electricity, this is how you should do it. You need a big lot and the backhoe will dig huge trenches everywhere. Superinsulation techniques would allow you to cut the size of the unit by half or more.
Air to air heat pumps, These are only efficient in milder climates. At temps below freezing, they become very inefficient because they have to use electric resistance heat to prevent frost build up. They are also expensive and complex to maintain, and run on electricity.
Ground water heat pumps, Also expensive, complex and requires at least two wells on the property, often against zoning regs to pump water back into the aquifer.
Outdoor wood furnaces, These have hideously poor efficiency, often less than 25%. The manufacturers often imply good efficiency, but you will universally find that they are short on indepent test data. They virtually all smoke (aka pollution) when operated as suggested in the ads. This is deforestation and pollution right in your own back yard.
Superinsulation. This is the best, period. I'm not biased or anything. Really.
So that's a thumbnail sketch of what is available, what works and what doesn't. I will support my wild claims for superinsulation in subsequent columns.
As far as actual progress on the actual house, nothing. Still fixing up the city house. Got about half of my cogenerator transfer switch unwired from the regular breaker box and will finish that tonight.
Finest regards,
troy
Friday, September 22, 2006
How to heat your house with cats.

My apologies for my tardiness. This is a big topic and I finally realized it’s just impossible to give it proper treatment in one column. So we will attack it piecewise.
How to heat your house with cats, or, in our case, a rabbit.
Most folks have noticed that energy has gotten expensive lately. This is true for gasoline, propane, natural gas, home heating oil and so on. It is also true that most folks do not expect this trend to be reversed any time soon, if ever. This issue has been in the media a lot lately in the form of Peak Oil theory, as originally described by King Hubbard. He was a brilliant petroleum geologist and geophysicist. For those who are curious, here’s a nice summary that avoids most of the hysteria associated with this idea:
http://en.wikipedia.org/wiki/Hubbert_peak
Some of the more extreme believers in this theory think that this phenomenon will cause 90% of the people on the planet to die in the next 20 years. Famines, wars, the whole end-of-the-world-as-we-know-it idea. Others believe in the “soft landing” theory, which suggests that this will just require some modest economic and lifestyle adjustments while we make the transition into renewable energy.
At this point, I have not entirely made up my mind which camp I am in, and for our immediate purposes, it doesn’t matter. The key issue is that energy is exquisitely unlikely to get cheap again. That doesn’t mean prices can’t wiggle up and down, but it will never go down very far for very long.
So, what shall we do about all this? I’m glad you asked because there’s a lot we can, should and must do. Today, we will learn about superinsulation techniques and someday, you will have the opportunity to put them into practice. Be warned, there will be resistance. But we will be prepared for it.
The people who build houses for a living are a pretty conservative lot. They like doing it the same way they have done it for decades. This will cause problems for you. Chances are pretty good that you will buy or build a house in the next ten years. Chances are also pretty good you will do some kind of remodeling on this house and/or the next. If you go along with the conservative building trades and the advice from the big box lumber store, this will cost you potentially many thousands of dollars in extra heating and cooling costs, and more importantly, you will waste irreplaceable energy resources.
Back in the day when coal was seven dollars a ton and home heating oil was ten cents a gallon, it just didn’t make economic sense to insulate your house. You would practically never recover your initial investment. Shoot, before the Second World War, residential insulation as we know it barely existed. Why would you bother when you could just put in a big ol’ furnace and shovel a little bit more coal. Everybody did it, and it was less work. Nobody really thought about the long term consequences. That was an unfortunate mistake caused by a short term and very narrow economic view of the situation.
Today, we just don’t have the luxury of being wasteful with non-renewable resources. Plus, I’m frugal. I am bothered by waste and I think it’s wrong, sinful even. I believe in stewardship. As a Christian, that means the resources aren’t really mine to waste anyway. God owns all the coal, all the oil, all the trees of the field, all the uranium and all my money to boot.
He loans all these resources to me and then tells me to do a first class job of taking care of his planet. Leave some for the next guy. Leave some for your great grandkids. Love your neighbor. Even love your enemy. He’s very clear on that. So that’s the motivation to conserve energy and resources. Now let’s talk about how to accomplish this.
Insulation is God’s gift to stewards like you and me. To get the basic idea about insulation, we have to talk about r-values. They are an objective measure of the ability of any particular insulation product to slow heat loss. The bigger the r-value, the better. We’ll deal with all the math and the subtleties in a subsequent column, but the short version says that if you double the r-values in a house, it suddenly takes half the energy to heat it.
This is where you will butt heads with your contractor. The vast majority of house builders only build two kinds of wall systems. For anything except the rich people who demand those new “energy efficient” houses, they build the walls using a single layer of 2x4’s. This is a very bad idea, because it physically limits the amount of insulation you can cram in there. For fiberglass, the most commonly used insulation, that means you theoretically get r-13. And the so called energy efficient model would use a 2x6 stud wall rather than the 2x4. That allows for a modest increase to approx r-20.
The hitch is, even this “energy efficient” model is not that well insulated when you consider the whole wall. Those r-values refer only to the insulating power of the material itself, not the whole wall as a finished product. The primary problem is that wood is not that great an insulator (r-1 per inch). With studs every 16” which is the standard, plus all the extra framing that is needed around corners, doors and windows, wood actually makes up 15-20% of the area of the wall. So effective insulation levels are right back to the underwhelming range of r-16. We need at least r-30.
To properly conserve our energy resources (which is a mandate from Almighty God don’t forget…) we want to install vast amounts of insulation into our walls. Almost magic things happen when you achieve r-30 to r-40 levels of insulation. Annual heat bills can be about the same size as monthly heat bills in a conventionally built house. Some heat their entire house using a largish water heater as a boiler for radiant floor heating or hot water baseboards. Conventional furnaces are often three times too big/powerful.
The tiniest EPA rated wood stove you can buy can successfully heat a 3,000 sq. ft. house with modest amounts of wood. Attaining this level of energy performance will require different kinds of insulation, or different kinds of wall framing systems, or both. Since it takes so little heat to keep the house comfortable, heat sources that we don’t ordinarily consider suddenly make a real difference.
Things like refrigerators, humans, light bulbs and cats all produce heat as a byproduct. Even the sunlight coming through the east, south and west windows can now make a significant contribution to making you comfortable in the winter. Taken together, these ambient or bonus heat sources may provide all the heat you need in the spring and fall. Who knew that you could make a passively solar heated house just by strapping enough insulation on there?
Your average general contractor will be resistant to most or all of these ideas. They will claim that nobody does it that way. They will say that it is very expensive. I had more than one contractor tell me it was outright stupid and that this was a big waste of time and money, and that ultimately it wouldn’t even work. They were all very wrong.
I would argue that all the opposites are true. Lots of people are building superinsulated houses. A Google search for “superinsulation” produced 38,000 hits, so somebody must be doing it. They are not that expensive initially and they are overwhelmingly less expensive in the long run. It’s true that you will spend more for framing and insulation, but you will need a much smaller furnace and probably no central air at all which offsets much of the cost.
As an example, I built a superinsulated house in the late 80's in Canada (pictured at top). The walls were 16 inches thick. We heated with propane (plus all the bonus heat!). When I first got the propane tank delivered, the propane company wanted to put me on automatic monthly fill ups during the winter to be sure I didn't run out. I commented that it was unlikely that I would use up even a single tank over the winter and they all laughed. It turned out to be true though, using approximately 1/3 of the propane used in a similar sized "energy efficient" house, and a tiny fraction of the propane needed by an old drafty farmhouse of similar size.
As a rule, these houses are highly successful and very comfortable to live in. It would almost be worth the extra cost and effort just for the amazing quiet that comes from thick well insulated walls. This concept is definitely worth pursuing since this strategy will save staggering amounts of energy over the lifespan of the house, and likely save you a pile of money as well. We will go into considerable detail over the next few entries about how to do this.
Most importantly, God will smile approvingly at your efforts to take care of His creation.
Finest regards,
troy and christina
Tuesday, September 05, 2006
Flirting with burnout?
On the surface, it really seems like I’ve been flirting with burnout. The Critical ToDo list only seems to get longer. Both my wife and I knew moving into this house was going to involve some serious time commitments. Here’s my current work list for the farmhouse:
-Build new exterior walls, just inside present walls
-New gutters and downspouts, along with drainage system
-All new wiring, including 2nd breaker panel and transfer switch
-Install Co-generation system, which I have to custom build
-Build and install insulated 5,000 gallon water tank in basement to store heat as part of co-gen system
-Install wood stove and insulated chimney, which goes through the first floor ceiling, the second floor ceiling and the roof
-Add fill dirt and re-grade around house to provide positive drainage away from house
-Plaster fieldstone basement walls with high strength, latex modified, fiber reinforced cement
-Cut, split, and stack firewood for this winter (very soon, has to properly season)
-Fix garage doors so we can actually park something in there
-Build some sort of temporary or permanent outbuilding to shelter the tractor and “new” Mercedes this winter
-Install 2 new exterior doors
-Fix and/or replace the present propane boiler so we don’t freeze to death this winter
-Winterize tractor, Chinese antifreeze not so reliable and looks nasty
-Add block heater to tractor so I can actually push snow with it this winter
-All new supply plumbing and all new plumbing fixtures
-Add insulation to new exterior stud walls
-Drywall everything
-Make floors level
-Install radiant floor heating system and tear out old baseboard radiators
-And some other stuff, some of which I’m not even aware of yet.
Much of this stuff is time/weather sensitive, so I have been busy like crazy. Several 14 hour days in a row are not uncommon. There are times when I am tempted to think I have bitten off more than I can chew. My regular job consumes 50 hours per week. I’m still remodeling the previous house so we can sell it and not run into cash flow problems. I still pick up used fryer oil from two restaurants that I use for my biodiesel.
I should be biting my fingernails right off. I should be sleeping poorly, I should be very highly stressed right now, what ever that means. Something...
I’m not.
This house feels right. That’s sort of a secular way of saying we believe we are being obedient to the will of God in making this move. Divining the will of God in a specific/personal way is a delicate business, but we think we are on the right track. If God wants me to do this, and I hold up my (almost insignificant) end of the deal, He will give me whatever resources, whatever time, whatever energy, whatever strength, whatever anything is necessary to get the job done. If God is for us, who can be against us?
Git 'er done.
troy
-Build new exterior walls, just inside present walls
-New gutters and downspouts, along with drainage system
-All new wiring, including 2nd breaker panel and transfer switch
-Install Co-generation system, which I have to custom build
-Build and install insulated 5,000 gallon water tank in basement to store heat as part of co-gen system
-Install wood stove and insulated chimney, which goes through the first floor ceiling, the second floor ceiling and the roof
-Add fill dirt and re-grade around house to provide positive drainage away from house
-Plaster fieldstone basement walls with high strength, latex modified, fiber reinforced cement
-Cut, split, and stack firewood for this winter (very soon, has to properly season)
-Fix garage doors so we can actually park something in there
-Build some sort of temporary or permanent outbuilding to shelter the tractor and “new” Mercedes this winter
-Install 2 new exterior doors
-Fix and/or replace the present propane boiler so we don’t freeze to death this winter
-Winterize tractor, Chinese antifreeze not so reliable and looks nasty
-Add block heater to tractor so I can actually push snow with it this winter
-All new supply plumbing and all new plumbing fixtures
-Add insulation to new exterior stud walls
-Drywall everything
-Make floors level
-Install radiant floor heating system and tear out old baseboard radiators
-And some other stuff, some of which I’m not even aware of yet.
Much of this stuff is time/weather sensitive, so I have been busy like crazy. Several 14 hour days in a row are not uncommon. There are times when I am tempted to think I have bitten off more than I can chew. My regular job consumes 50 hours per week. I’m still remodeling the previous house so we can sell it and not run into cash flow problems. I still pick up used fryer oil from two restaurants that I use for my biodiesel.
I should be biting my fingernails right off. I should be sleeping poorly, I should be very highly stressed right now, what ever that means. Something...
I’m not.
This house feels right. That’s sort of a secular way of saying we believe we are being obedient to the will of God in making this move. Divining the will of God in a specific/personal way is a delicate business, but we think we are on the right track. If God wants me to do this, and I hold up my (almost insignificant) end of the deal, He will give me whatever resources, whatever time, whatever energy, whatever strength, whatever anything is necessary to get the job done. If God is for us, who can be against us?
Git 'er done.
troy
Friday, August 25, 2006
The joys of drywall and deer
Not a lot happened with the farm house this week, so for those looking strictly for updates, you may as well pack it in now. I won’t get a lot of work done on the farm house until the city house is fully refurbished and ready for sale. Hopefully, that will be two or three weeks. My day job really interferes with my ability to get work done. I am completely mystified at people who can watch television 20-40+ hours per week.
I guess I did receive my scaffolding which is mostly set up at the new house. The bid to put gutters on the house and garage was almost $1,400. Five hundred dollars worth of scaffolding suddenly looks like a bargain. Materials cost for the gutters will run about $300. Plus I get “free” scaffolding out of the deal.
I picked up all the supplies to hook up the sump pump. If I’m too tired to do actual work, I can at least go shopping.
We do have some deer that drop by every day to check on progress at the house. Mostly, they check out the corn that I put out for them, and the salt block. The most frequent visitors are a young doe and her even younger fawn, still with a few fading white spots. I was watching them work on the salt block yesterday morning. Deer have amazingly long tongues. I use binoculars sometimes, though they are scarcely fifty feet behind the house.
Even though deer are pretty and I like having them around, I intend to shoot a couple this fall. Venison is tasty, naturally lean and low in cholesterol. Of course it’s organic in the sense that they don’t get growth hormones and antibiotics in their feed. Deer cost farmers millions of dollars a year in crop damage. The deer population in this state could use a lot of thinning out anyway. Failure to do that will cause lots of deer to starve to death this winter and increase the risk for a big die off from Chronic Wasting Disease (the deer version of Mad Cow disease) and other disease issues.
Despite the fact that not a lot of things happened at the country house, other things did happen. I finished the repair of the plaster work (on the city house) in the living room, dining room and office, praise the Lord oh my soul!
I’m not fast at drywall/plaster work. This is probably due to the fact that I don’t hang or finish drywall for a living. The finished product is top quality though. On the whole, I think this is not a bad trade off. I would be miserable doing this 8-10 hours a day. The way it stands now, I actually have moments when I can disregard the aching shoulders, the choking dust, the filthy hair and clothes and the grit in my eye. I can find satisfaction and even joy in making a broken, rough surface into something that is smooth and satisfying to the eye and the hand.
I attribute this joy to the fact that we are made in the image of God. We all find pleasure in fixing things that need it, unless we are deeply separated from our maker. It could be the car, the house, the research paper, the kids’ toys, mending clothes or the relationship with our spouse. We all have our area of expertise. But He is the great fixer, and will ultimately right every wrong.
Have an exceptionally good week.
troy
I guess I did receive my scaffolding which is mostly set up at the new house. The bid to put gutters on the house and garage was almost $1,400. Five hundred dollars worth of scaffolding suddenly looks like a bargain. Materials cost for the gutters will run about $300. Plus I get “free” scaffolding out of the deal.
I picked up all the supplies to hook up the sump pump. If I’m too tired to do actual work, I can at least go shopping.
We do have some deer that drop by every day to check on progress at the house. Mostly, they check out the corn that I put out for them, and the salt block. The most frequent visitors are a young doe and her even younger fawn, still with a few fading white spots. I was watching them work on the salt block yesterday morning. Deer have amazingly long tongues. I use binoculars sometimes, though they are scarcely fifty feet behind the house.
Even though deer are pretty and I like having them around, I intend to shoot a couple this fall. Venison is tasty, naturally lean and low in cholesterol. Of course it’s organic in the sense that they don’t get growth hormones and antibiotics in their feed. Deer cost farmers millions of dollars a year in crop damage. The deer population in this state could use a lot of thinning out anyway. Failure to do that will cause lots of deer to starve to death this winter and increase the risk for a big die off from Chronic Wasting Disease (the deer version of Mad Cow disease) and other disease issues.
Despite the fact that not a lot of things happened at the country house, other things did happen. I finished the repair of the plaster work (on the city house) in the living room, dining room and office, praise the Lord oh my soul!
I’m not fast at drywall/plaster work. This is probably due to the fact that I don’t hang or finish drywall for a living. The finished product is top quality though. On the whole, I think this is not a bad trade off. I would be miserable doing this 8-10 hours a day. The way it stands now, I actually have moments when I can disregard the aching shoulders, the choking dust, the filthy hair and clothes and the grit in my eye. I can find satisfaction and even joy in making a broken, rough surface into something that is smooth and satisfying to the eye and the hand.
I attribute this joy to the fact that we are made in the image of God. We all find pleasure in fixing things that need it, unless we are deeply separated from our maker. It could be the car, the house, the research paper, the kids’ toys, mending clothes or the relationship with our spouse. We all have our area of expertise. But He is the great fixer, and will ultimately right every wrong.
Have an exceptionally good week.
troy
Saturday, August 19, 2006
There really is right and wrong, or, why my basement leaks.
I am a pretty orthodox Christian. My view of the world includes a deeply embedded conviction that there really is a right and a wrong. I think most rational people, even non-Christians, recognize from their experience with the world, that there are good ways and bad ways of getting through life.
My basement is a testament to that.
It leaks like a proverbial sieve every time it rains, with water literally gushing down the fieldstone walls. (It rained pretty steadily last night, which was the impetus for this blog...) It need not be so, and I will make it so that it is not so. I hate wet basements. They are worse than useless. I'm not sure why I have such an aversion to damp, stinky basements. It could be because the house I grew up in had a wet basement, and my job was to dry it out periodically. This involved sponges and dust pans and buckets, and was generally quite unsuccessful, since the root cause was never addressed.
The root cause at my house ultimately harks back to original sin. People just didn't do what they were supposed to do.
When the house was originally built, the basement was probably not wet. The house sits up on a nice hill. We have nice sandy soil with minimal clay so it should drain well. The house probably had gutters and downspouts that worked to get the rainwater away from the foundation. Over the last hundred years or so, neglect and laziness have fouled things up.
The back-filled soil around the foundation settled 4-6 inches, which is pretty typical. So instead of the ground sloping away from the house, it now slopes toward the foundation. That by itself is pretty much guaranteed to cause a damp basement. Observant, stewardly and faithful owners would have noticed this decades ago and brought in some topsoil to produce some slope and positive drainage away from the house.
Compounding that problem, the roof was replaced a few years ago. So far as I can tell, they did a good job on the roof. Well, they did use waferboard to repair the roof sheathing in places, and waferboard is the invention of the devil. So long as you keep it dry it's ok. If it gets wet just a few times, it swell up and exhibits all of the strength of wet oatmeal. Effectively, waferboard is laminated corn flakes. The glues used to make little bitty pieces of wood into one big piece of "wood" virtually all contain formaldahyde and other nasties. Never use waferboard inside your house where you will be breathing the gasses released for years by this evil product. The only thing worse than waferboard is particleboard, but I digress.
The flagrant sin that the roofer commited is that he took most of the gutters and downspouts off to do the roof, and then just decided he didn't need to replace them. This causes the considerable volume of rainwater intercepted by the roof to be very efficiently channeled to fall on the ground right next to the foundation, where it can't get away because the ground slopes toward the house. Thus the cesspool that is my basement.
There are several steps that we will take to insure a clean dry, stink free and useful basement:
1. New gutters and downspouts, lots of them. Our house is practically the house of seven gables. I have 2 1/2 stories of scaffolding on order, should be in next week.
2. The downspouts will feed into pipes in the ground that take the runoff far away from the foundation using non-perforated pipe, and then switch to "Big-O" perforated pipe to harmlessly percolate the water into the ground where it belongs. Of course, all those pipes have to be installed in the yard, which means backhoe and tractor work. Wooo hoooo! The "Miss Dig" person has flagged and painted our yard this week, indicating it is ok to dig away.
These two steps alone will solve 80% of the problem at least.
3. Seven cubic yards of screened topsoil will be added around the foundation to improve natural drainage away from the house. This should fix the other 20%.
If those three steps don't entirely fix the problem, then we get out the big guns:
4. Trench the yard (lots and lots of backhoe work) on both sides of the house and install Big-O and effectively lower the water table below the basement floor. The farmers call this tiling the field because they used to use 3' sections of clay tile (pipe) to do the job. This will be unneccessary. I have made a couple of test holes to see how damp things are and see if we have a very high/problematic water table. We don't.
5. Dig up all the dirt from around the foundation and plaster the fieldstone foundation with high strength fiber reinforced concrete. This will make the foundation itself much less water permeable. The new cement is then typically painted with either rubber based glop or ashphalt based glop. Foundation drains would be installed below the footings all the way around the house and connected to a drain that heads downhill at 0.25 inches per foot until it pops out the side of the hill 75 feet away.
Step 5 will solve all water problems in all basements of all houses that sit up on a hill, asuming the gutters work. Even though this would involve lots of fun work with the backhoe and front end loader, it's a last resort because it will suck up vast quantities of time.
Whatever trivial dampness remains after all this will be rapidly and efficiently removed by the dehumidifyer. After insulating the basement, even humidity problems will be a thing of the past.
I will try to post weekly updates on Friday or Saturday.
Finest regards
troy
My basement is a testament to that.
It leaks like a proverbial sieve every time it rains, with water literally gushing down the fieldstone walls. (It rained pretty steadily last night, which was the impetus for this blog...) It need not be so, and I will make it so that it is not so. I hate wet basements. They are worse than useless. I'm not sure why I have such an aversion to damp, stinky basements. It could be because the house I grew up in had a wet basement, and my job was to dry it out periodically. This involved sponges and dust pans and buckets, and was generally quite unsuccessful, since the root cause was never addressed.
The root cause at my house ultimately harks back to original sin. People just didn't do what they were supposed to do.
When the house was originally built, the basement was probably not wet. The house sits up on a nice hill. We have nice sandy soil with minimal clay so it should drain well. The house probably had gutters and downspouts that worked to get the rainwater away from the foundation. Over the last hundred years or so, neglect and laziness have fouled things up.
The back-filled soil around the foundation settled 4-6 inches, which is pretty typical. So instead of the ground sloping away from the house, it now slopes toward the foundation. That by itself is pretty much guaranteed to cause a damp basement. Observant, stewardly and faithful owners would have noticed this decades ago and brought in some topsoil to produce some slope and positive drainage away from the house.
Compounding that problem, the roof was replaced a few years ago. So far as I can tell, they did a good job on the roof. Well, they did use waferboard to repair the roof sheathing in places, and waferboard is the invention of the devil. So long as you keep it dry it's ok. If it gets wet just a few times, it swell up and exhibits all of the strength of wet oatmeal. Effectively, waferboard is laminated corn flakes. The glues used to make little bitty pieces of wood into one big piece of "wood" virtually all contain formaldahyde and other nasties. Never use waferboard inside your house where you will be breathing the gasses released for years by this evil product. The only thing worse than waferboard is particleboard, but I digress.
The flagrant sin that the roofer commited is that he took most of the gutters and downspouts off to do the roof, and then just decided he didn't need to replace them. This causes the considerable volume of rainwater intercepted by the roof to be very efficiently channeled to fall on the ground right next to the foundation, where it can't get away because the ground slopes toward the house. Thus the cesspool that is my basement.
There are several steps that we will take to insure a clean dry, stink free and useful basement:
1. New gutters and downspouts, lots of them. Our house is practically the house of seven gables. I have 2 1/2 stories of scaffolding on order, should be in next week.
2. The downspouts will feed into pipes in the ground that take the runoff far away from the foundation using non-perforated pipe, and then switch to "Big-O" perforated pipe to harmlessly percolate the water into the ground where it belongs. Of course, all those pipes have to be installed in the yard, which means backhoe and tractor work. Wooo hoooo! The "Miss Dig" person has flagged and painted our yard this week, indicating it is ok to dig away.
These two steps alone will solve 80% of the problem at least.
3. Seven cubic yards of screened topsoil will be added around the foundation to improve natural drainage away from the house. This should fix the other 20%.
If those three steps don't entirely fix the problem, then we get out the big guns:
4. Trench the yard (lots and lots of backhoe work) on both sides of the house and install Big-O and effectively lower the water table below the basement floor. The farmers call this tiling the field because they used to use 3' sections of clay tile (pipe) to do the job. This will be unneccessary. I have made a couple of test holes to see how damp things are and see if we have a very high/problematic water table. We don't.
5. Dig up all the dirt from around the foundation and plaster the fieldstone foundation with high strength fiber reinforced concrete. This will make the foundation itself much less water permeable. The new cement is then typically painted with either rubber based glop or ashphalt based glop. Foundation drains would be installed below the footings all the way around the house and connected to a drain that heads downhill at 0.25 inches per foot until it pops out the side of the hill 75 feet away.
Step 5 will solve all water problems in all basements of all houses that sit up on a hill, asuming the gutters work. Even though this would involve lots of fun work with the backhoe and front end loader, it's a last resort because it will suck up vast quantities of time.
Whatever trivial dampness remains after all this will be rapidly and efficiently removed by the dehumidifyer. After insulating the basement, even humidity problems will be a thing of the past.
I will try to post weekly updates on Friday or Saturday.
Finest regards
troy
Monday, August 07, 2006
Using a crowbar with finesse...
Moving for most families is not a pleasant experience. There are those rich few who hire professionals to do it all; take down, packing, transport, unpacking and setup. It costs a fortune (and I am a frugal tightwad...) and there are still all too many stories of things gone wrong. So my wife and I are stuck doing it without the use of professionals. Our small group has helped mightily, for which we are very grateful.
Moving my particular chatels and baggage is especially problematic because I have a basement full of tools and machines, some of which weigh well over half a ton. Of course, the long term solution is an above ground shop, but that will have to wait a bit. In the mean time, all those cast iron beasties will have to be dragged out of the basement, transported 30 miles, and dragged into the new basement.
This brings us to the crux of the post. The "new" house has an abominable set of stairs into the basement. They used 2x6's for treads and stringers and they put the accursed thing in the most inaccessible spot on the first floor. It is very steep and there's not enough head room and they are weak. It is essentially useless for moving lathes and milling machines and large diesel engines. So, we determined to reinstall the other stairs and matching exterior door that the house was originally equiped with. To accomplish that, we had to tear a hole in the floor and remove the old door, which was nailed shut and covered with paneling on the inside and plywood on the outside.
The tool of choice for some of these impediments is a crowbar. A crowbar does not look impressive or complex. As far as tools go, it looks one small step above a rock in complexity. After all, it's just a steel rod about the size of a man's thumb, with a gentle hook on one end and something less than three feet long. Both ends have a little wedge shape. How hard can it be to use a crowbar?
In the hands of an unthinking cad, a crowbar is a weapon of mass destruction which will cause vast amounts of collateral damage, both to the building and to whatever innocent bystanders are available. The cad himself is often injured as well.
However, in the hands of a master, a crowbar can deliver almost surgical precision in the deconstruction of a stick built house. Joel is such an artist. He wields the bar with such finnesse as to provide precisely the neccessary level of destruction, and no more.
I take my hat off to him.
We won't discuss the fact that we were both whumpstugled for two hours while trying to compute the correct geometry for the new stair stringers. Plus we had to account for the fact that the finished floor upstairs will be three inches taller, while the basement floor will end up one or two inches higher. Yet, in the end, we overcame the geometry.
How would Jesus compute stair stringers I wonder? Did he have to look things over for a while and contemplate, measure some things, do math, then contemplate some more? Or did he just know?
troy
Moving my particular chatels and baggage is especially problematic because I have a basement full of tools and machines, some of which weigh well over half a ton. Of course, the long term solution is an above ground shop, but that will have to wait a bit. In the mean time, all those cast iron beasties will have to be dragged out of the basement, transported 30 miles, and dragged into the new basement.
This brings us to the crux of the post. The "new" house has an abominable set of stairs into the basement. They used 2x6's for treads and stringers and they put the accursed thing in the most inaccessible spot on the first floor. It is very steep and there's not enough head room and they are weak. It is essentially useless for moving lathes and milling machines and large diesel engines. So, we determined to reinstall the other stairs and matching exterior door that the house was originally equiped with. To accomplish that, we had to tear a hole in the floor and remove the old door, which was nailed shut and covered with paneling on the inside and plywood on the outside.
The tool of choice for some of these impediments is a crowbar. A crowbar does not look impressive or complex. As far as tools go, it looks one small step above a rock in complexity. After all, it's just a steel rod about the size of a man's thumb, with a gentle hook on one end and something less than three feet long. Both ends have a little wedge shape. How hard can it be to use a crowbar?
In the hands of an unthinking cad, a crowbar is a weapon of mass destruction which will cause vast amounts of collateral damage, both to the building and to whatever innocent bystanders are available. The cad himself is often injured as well.
However, in the hands of a master, a crowbar can deliver almost surgical precision in the deconstruction of a stick built house. Joel is such an artist. He wields the bar with such finnesse as to provide precisely the neccessary level of destruction, and no more.
I take my hat off to him.
We won't discuss the fact that we were both whumpstugled for two hours while trying to compute the correct geometry for the new stair stringers. Plus we had to account for the fact that the finished floor upstairs will be three inches taller, while the basement floor will end up one or two inches higher. Yet, in the end, we overcame the geometry.
How would Jesus compute stair stringers I wonder? Did he have to look things over for a while and contemplate, measure some things, do math, then contemplate some more? Or did he just know?
troy
Friday, August 04, 2006
Introductions and generalities
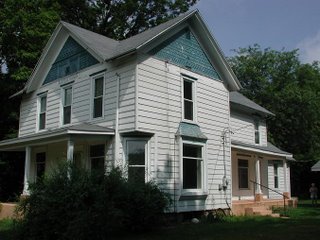
Welcome to the blog.
My wife and I purchased an old farm house with the intent to make it a showcase for energy efficiency and super insulation remodeling techniques. We hope to have several ways of heating the house, including efficient wood heat, radiant floors, biodiesel co-generation, propane boiler (backup) and electric (from the generator). When we are finished, the house should use approximately 1/3 the energy of a new conventional house, and 1/10 the energy of the original setup. We will document our progress for your enjoyment and edification.
Don't expect a slam/bam, spend a hundred grand and poof, one month later you get to see the cool remodel, like one of those TV programs. Since we both work full time, this will be a slow, if not leisurely process.
Photos will appear as time goes on.
We are fortunate that the exterior of the house does not need any immediate work other than gutters. The interior however is terrible. The floors are badly out of level due to settling. The wiring is a scary joke with one very worn out receptacle in each room. There is no grounding. The heating system may or may not work. The "decorating" is from the Nixon era I think. We have many peculiar shades of shag carpeting upstairs and several hideous kinds of vinyl tile downstairs. Several rooms on the main floor have icky suspended ceilings which will all have to be torn out.
The basement is very damp and stinky. That is very high on the list of things to do. I will have to dig a trench all the way around the outside foundation (which is lovely fieldstone) and add drainage pipe. Since we sit on top of a nice hill, it should be easy to run the drains downhill until they exit the hillside. Then we won't be dependent on a sump pump as it will all drain by gravity. Any excuse to run the new tractor/backhoe is OK by me.
I was afraid that we would have zero insulation, but that turns out to be an unfounded concern. Someone in the past put blown-in cellulose in the walls so I won't have to do that at least. We will add additional insulation by adding a second layer of framing to double the thickness of the exterior walls. This will primarily be done on the inside, since most of the rooms are big enough to lose 4-6 inches on the exterior wall.
If I stay reasonably motivated, this should all be finished in time for the big 50th birthday party, which is 4 years hence.
Finest regards,
troy and christina
Subscribe to:
Posts (Atom)