Not a lot happened with the farm house this week, so for those looking strictly for updates, you may as well pack it in now. I won’t get a lot of work done on the farm house until the city house is fully refurbished and ready for sale. Hopefully, that will be two or three weeks. My day job really interferes with my ability to get work done. I am completely mystified at people who can watch television 20-40+ hours per week.
I guess I did receive my scaffolding which is mostly set up at the new house. The bid to put gutters on the house and garage was almost $1,400. Five hundred dollars worth of scaffolding suddenly looks like a bargain. Materials cost for the gutters will run about $300. Plus I get “free” scaffolding out of the deal.
I picked up all the supplies to hook up the sump pump. If I’m too tired to do actual work, I can at least go shopping.
We do have some deer that drop by every day to check on progress at the house. Mostly, they check out the corn that I put out for them, and the salt block. The most frequent visitors are a young doe and her even younger fawn, still with a few fading white spots. I was watching them work on the salt block yesterday morning. Deer have amazingly long tongues. I use binoculars sometimes, though they are scarcely fifty feet behind the house.
Even though deer are pretty and I like having them around, I intend to shoot a couple this fall. Venison is tasty, naturally lean and low in cholesterol. Of course it’s organic in the sense that they don’t get growth hormones and antibiotics in their feed. Deer cost farmers millions of dollars a year in crop damage. The deer population in this state could use a lot of thinning out anyway. Failure to do that will cause lots of deer to starve to death this winter and increase the risk for a big die off from Chronic Wasting Disease (the deer version of Mad Cow disease) and other disease issues.
Despite the fact that not a lot of things happened at the country house, other things did happen. I finished the repair of the plaster work (on the city house) in the living room, dining room and office, praise the Lord oh my soul!
I’m not fast at drywall/plaster work. This is probably due to the fact that I don’t hang or finish drywall for a living. The finished product is top quality though. On the whole, I think this is not a bad trade off. I would be miserable doing this 8-10 hours a day. The way it stands now, I actually have moments when I can disregard the aching shoulders, the choking dust, the filthy hair and clothes and the grit in my eye. I can find satisfaction and even joy in making a broken, rough surface into something that is smooth and satisfying to the eye and the hand.
I attribute this joy to the fact that we are made in the image of God. We all find pleasure in fixing things that need it, unless we are deeply separated from our maker. It could be the car, the house, the research paper, the kids’ toys, mending clothes or the relationship with our spouse. We all have our area of expertise. But He is the great fixer, and will ultimately right every wrong.
Have an exceptionally good week.
troy
The process of converting a lovely old farmhouse into an efficient cheap-to-heat comfortable home and the life we lead while doing it.
Friday, August 25, 2006
Saturday, August 19, 2006
There really is right and wrong, or, why my basement leaks.
I am a pretty orthodox Christian. My view of the world includes a deeply embedded conviction that there really is a right and a wrong. I think most rational people, even non-Christians, recognize from their experience with the world, that there are good ways and bad ways of getting through life.
My basement is a testament to that.
It leaks like a proverbial sieve every time it rains, with water literally gushing down the fieldstone walls. (It rained pretty steadily last night, which was the impetus for this blog...) It need not be so, and I will make it so that it is not so. I hate wet basements. They are worse than useless. I'm not sure why I have such an aversion to damp, stinky basements. It could be because the house I grew up in had a wet basement, and my job was to dry it out periodically. This involved sponges and dust pans and buckets, and was generally quite unsuccessful, since the root cause was never addressed.
The root cause at my house ultimately harks back to original sin. People just didn't do what they were supposed to do.
When the house was originally built, the basement was probably not wet. The house sits up on a nice hill. We have nice sandy soil with minimal clay so it should drain well. The house probably had gutters and downspouts that worked to get the rainwater away from the foundation. Over the last hundred years or so, neglect and laziness have fouled things up.
The back-filled soil around the foundation settled 4-6 inches, which is pretty typical. So instead of the ground sloping away from the house, it now slopes toward the foundation. That by itself is pretty much guaranteed to cause a damp basement. Observant, stewardly and faithful owners would have noticed this decades ago and brought in some topsoil to produce some slope and positive drainage away from the house.
Compounding that problem, the roof was replaced a few years ago. So far as I can tell, they did a good job on the roof. Well, they did use waferboard to repair the roof sheathing in places, and waferboard is the invention of the devil. So long as you keep it dry it's ok. If it gets wet just a few times, it swell up and exhibits all of the strength of wet oatmeal. Effectively, waferboard is laminated corn flakes. The glues used to make little bitty pieces of wood into one big piece of "wood" virtually all contain formaldahyde and other nasties. Never use waferboard inside your house where you will be breathing the gasses released for years by this evil product. The only thing worse than waferboard is particleboard, but I digress.
The flagrant sin that the roofer commited is that he took most of the gutters and downspouts off to do the roof, and then just decided he didn't need to replace them. This causes the considerable volume of rainwater intercepted by the roof to be very efficiently channeled to fall on the ground right next to the foundation, where it can't get away because the ground slopes toward the house. Thus the cesspool that is my basement.
There are several steps that we will take to insure a clean dry, stink free and useful basement:
1. New gutters and downspouts, lots of them. Our house is practically the house of seven gables. I have 2 1/2 stories of scaffolding on order, should be in next week.
2. The downspouts will feed into pipes in the ground that take the runoff far away from the foundation using non-perforated pipe, and then switch to "Big-O" perforated pipe to harmlessly percolate the water into the ground where it belongs. Of course, all those pipes have to be installed in the yard, which means backhoe and tractor work. Wooo hoooo! The "Miss Dig" person has flagged and painted our yard this week, indicating it is ok to dig away.
These two steps alone will solve 80% of the problem at least.
3. Seven cubic yards of screened topsoil will be added around the foundation to improve natural drainage away from the house. This should fix the other 20%.
If those three steps don't entirely fix the problem, then we get out the big guns:
4. Trench the yard (lots and lots of backhoe work) on both sides of the house and install Big-O and effectively lower the water table below the basement floor. The farmers call this tiling the field because they used to use 3' sections of clay tile (pipe) to do the job. This will be unneccessary. I have made a couple of test holes to see how damp things are and see if we have a very high/problematic water table. We don't.
5. Dig up all the dirt from around the foundation and plaster the fieldstone foundation with high strength fiber reinforced concrete. This will make the foundation itself much less water permeable. The new cement is then typically painted with either rubber based glop or ashphalt based glop. Foundation drains would be installed below the footings all the way around the house and connected to a drain that heads downhill at 0.25 inches per foot until it pops out the side of the hill 75 feet away.
Step 5 will solve all water problems in all basements of all houses that sit up on a hill, asuming the gutters work. Even though this would involve lots of fun work with the backhoe and front end loader, it's a last resort because it will suck up vast quantities of time.
Whatever trivial dampness remains after all this will be rapidly and efficiently removed by the dehumidifyer. After insulating the basement, even humidity problems will be a thing of the past.
I will try to post weekly updates on Friday or Saturday.
Finest regards
troy
My basement is a testament to that.
It leaks like a proverbial sieve every time it rains, with water literally gushing down the fieldstone walls. (It rained pretty steadily last night, which was the impetus for this blog...) It need not be so, and I will make it so that it is not so. I hate wet basements. They are worse than useless. I'm not sure why I have such an aversion to damp, stinky basements. It could be because the house I grew up in had a wet basement, and my job was to dry it out periodically. This involved sponges and dust pans and buckets, and was generally quite unsuccessful, since the root cause was never addressed.
The root cause at my house ultimately harks back to original sin. People just didn't do what they were supposed to do.
When the house was originally built, the basement was probably not wet. The house sits up on a nice hill. We have nice sandy soil with minimal clay so it should drain well. The house probably had gutters and downspouts that worked to get the rainwater away from the foundation. Over the last hundred years or so, neglect and laziness have fouled things up.
The back-filled soil around the foundation settled 4-6 inches, which is pretty typical. So instead of the ground sloping away from the house, it now slopes toward the foundation. That by itself is pretty much guaranteed to cause a damp basement. Observant, stewardly and faithful owners would have noticed this decades ago and brought in some topsoil to produce some slope and positive drainage away from the house.
Compounding that problem, the roof was replaced a few years ago. So far as I can tell, they did a good job on the roof. Well, they did use waferboard to repair the roof sheathing in places, and waferboard is the invention of the devil. So long as you keep it dry it's ok. If it gets wet just a few times, it swell up and exhibits all of the strength of wet oatmeal. Effectively, waferboard is laminated corn flakes. The glues used to make little bitty pieces of wood into one big piece of "wood" virtually all contain formaldahyde and other nasties. Never use waferboard inside your house where you will be breathing the gasses released for years by this evil product. The only thing worse than waferboard is particleboard, but I digress.
The flagrant sin that the roofer commited is that he took most of the gutters and downspouts off to do the roof, and then just decided he didn't need to replace them. This causes the considerable volume of rainwater intercepted by the roof to be very efficiently channeled to fall on the ground right next to the foundation, where it can't get away because the ground slopes toward the house. Thus the cesspool that is my basement.
There are several steps that we will take to insure a clean dry, stink free and useful basement:
1. New gutters and downspouts, lots of them. Our house is practically the house of seven gables. I have 2 1/2 stories of scaffolding on order, should be in next week.
2. The downspouts will feed into pipes in the ground that take the runoff far away from the foundation using non-perforated pipe, and then switch to "Big-O" perforated pipe to harmlessly percolate the water into the ground where it belongs. Of course, all those pipes have to be installed in the yard, which means backhoe and tractor work. Wooo hoooo! The "Miss Dig" person has flagged and painted our yard this week, indicating it is ok to dig away.
These two steps alone will solve 80% of the problem at least.
3. Seven cubic yards of screened topsoil will be added around the foundation to improve natural drainage away from the house. This should fix the other 20%.
If those three steps don't entirely fix the problem, then we get out the big guns:
4. Trench the yard (lots and lots of backhoe work) on both sides of the house and install Big-O and effectively lower the water table below the basement floor. The farmers call this tiling the field because they used to use 3' sections of clay tile (pipe) to do the job. This will be unneccessary. I have made a couple of test holes to see how damp things are and see if we have a very high/problematic water table. We don't.
5. Dig up all the dirt from around the foundation and plaster the fieldstone foundation with high strength fiber reinforced concrete. This will make the foundation itself much less water permeable. The new cement is then typically painted with either rubber based glop or ashphalt based glop. Foundation drains would be installed below the footings all the way around the house and connected to a drain that heads downhill at 0.25 inches per foot until it pops out the side of the hill 75 feet away.
Step 5 will solve all water problems in all basements of all houses that sit up on a hill, asuming the gutters work. Even though this would involve lots of fun work with the backhoe and front end loader, it's a last resort because it will suck up vast quantities of time.
Whatever trivial dampness remains after all this will be rapidly and efficiently removed by the dehumidifyer. After insulating the basement, even humidity problems will be a thing of the past.
I will try to post weekly updates on Friday or Saturday.
Finest regards
troy
Monday, August 07, 2006
Using a crowbar with finesse...
Moving for most families is not a pleasant experience. There are those rich few who hire professionals to do it all; take down, packing, transport, unpacking and setup. It costs a fortune (and I am a frugal tightwad...) and there are still all too many stories of things gone wrong. So my wife and I are stuck doing it without the use of professionals. Our small group has helped mightily, for which we are very grateful.
Moving my particular chatels and baggage is especially problematic because I have a basement full of tools and machines, some of which weigh well over half a ton. Of course, the long term solution is an above ground shop, but that will have to wait a bit. In the mean time, all those cast iron beasties will have to be dragged out of the basement, transported 30 miles, and dragged into the new basement.
This brings us to the crux of the post. The "new" house has an abominable set of stairs into the basement. They used 2x6's for treads and stringers and they put the accursed thing in the most inaccessible spot on the first floor. It is very steep and there's not enough head room and they are weak. It is essentially useless for moving lathes and milling machines and large diesel engines. So, we determined to reinstall the other stairs and matching exterior door that the house was originally equiped with. To accomplish that, we had to tear a hole in the floor and remove the old door, which was nailed shut and covered with paneling on the inside and plywood on the outside.
The tool of choice for some of these impediments is a crowbar. A crowbar does not look impressive or complex. As far as tools go, it looks one small step above a rock in complexity. After all, it's just a steel rod about the size of a man's thumb, with a gentle hook on one end and something less than three feet long. Both ends have a little wedge shape. How hard can it be to use a crowbar?
In the hands of an unthinking cad, a crowbar is a weapon of mass destruction which will cause vast amounts of collateral damage, both to the building and to whatever innocent bystanders are available. The cad himself is often injured as well.
However, in the hands of a master, a crowbar can deliver almost surgical precision in the deconstruction of a stick built house. Joel is such an artist. He wields the bar with such finnesse as to provide precisely the neccessary level of destruction, and no more.
I take my hat off to him.
We won't discuss the fact that we were both whumpstugled for two hours while trying to compute the correct geometry for the new stair stringers. Plus we had to account for the fact that the finished floor upstairs will be three inches taller, while the basement floor will end up one or two inches higher. Yet, in the end, we overcame the geometry.
How would Jesus compute stair stringers I wonder? Did he have to look things over for a while and contemplate, measure some things, do math, then contemplate some more? Or did he just know?
troy
Moving my particular chatels and baggage is especially problematic because I have a basement full of tools and machines, some of which weigh well over half a ton. Of course, the long term solution is an above ground shop, but that will have to wait a bit. In the mean time, all those cast iron beasties will have to be dragged out of the basement, transported 30 miles, and dragged into the new basement.
This brings us to the crux of the post. The "new" house has an abominable set of stairs into the basement. They used 2x6's for treads and stringers and they put the accursed thing in the most inaccessible spot on the first floor. It is very steep and there's not enough head room and they are weak. It is essentially useless for moving lathes and milling machines and large diesel engines. So, we determined to reinstall the other stairs and matching exterior door that the house was originally equiped with. To accomplish that, we had to tear a hole in the floor and remove the old door, which was nailed shut and covered with paneling on the inside and plywood on the outside.
The tool of choice for some of these impediments is a crowbar. A crowbar does not look impressive or complex. As far as tools go, it looks one small step above a rock in complexity. After all, it's just a steel rod about the size of a man's thumb, with a gentle hook on one end and something less than three feet long. Both ends have a little wedge shape. How hard can it be to use a crowbar?
In the hands of an unthinking cad, a crowbar is a weapon of mass destruction which will cause vast amounts of collateral damage, both to the building and to whatever innocent bystanders are available. The cad himself is often injured as well.
However, in the hands of a master, a crowbar can deliver almost surgical precision in the deconstruction of a stick built house. Joel is such an artist. He wields the bar with such finnesse as to provide precisely the neccessary level of destruction, and no more.
I take my hat off to him.
We won't discuss the fact that we were both whumpstugled for two hours while trying to compute the correct geometry for the new stair stringers. Plus we had to account for the fact that the finished floor upstairs will be three inches taller, while the basement floor will end up one or two inches higher. Yet, in the end, we overcame the geometry.
How would Jesus compute stair stringers I wonder? Did he have to look things over for a while and contemplate, measure some things, do math, then contemplate some more? Or did he just know?
troy
Friday, August 04, 2006
Introductions and generalities
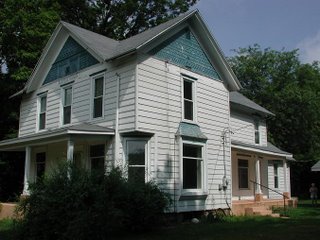
Welcome to the blog.
My wife and I purchased an old farm house with the intent to make it a showcase for energy efficiency and super insulation remodeling techniques. We hope to have several ways of heating the house, including efficient wood heat, radiant floors, biodiesel co-generation, propane boiler (backup) and electric (from the generator). When we are finished, the house should use approximately 1/3 the energy of a new conventional house, and 1/10 the energy of the original setup. We will document our progress for your enjoyment and edification.
Don't expect a slam/bam, spend a hundred grand and poof, one month later you get to see the cool remodel, like one of those TV programs. Since we both work full time, this will be a slow, if not leisurely process.
Photos will appear as time goes on.
We are fortunate that the exterior of the house does not need any immediate work other than gutters. The interior however is terrible. The floors are badly out of level due to settling. The wiring is a scary joke with one very worn out receptacle in each room. There is no grounding. The heating system may or may not work. The "decorating" is from the Nixon era I think. We have many peculiar shades of shag carpeting upstairs and several hideous kinds of vinyl tile downstairs. Several rooms on the main floor have icky suspended ceilings which will all have to be torn out.
The basement is very damp and stinky. That is very high on the list of things to do. I will have to dig a trench all the way around the outside foundation (which is lovely fieldstone) and add drainage pipe. Since we sit on top of a nice hill, it should be easy to run the drains downhill until they exit the hillside. Then we won't be dependent on a sump pump as it will all drain by gravity. Any excuse to run the new tractor/backhoe is OK by me.
I was afraid that we would have zero insulation, but that turns out to be an unfounded concern. Someone in the past put blown-in cellulose in the walls so I won't have to do that at least. We will add additional insulation by adding a second layer of framing to double the thickness of the exterior walls. This will primarily be done on the inside, since most of the rooms are big enough to lose 4-6 inches on the exterior wall.
If I stay reasonably motivated, this should all be finished in time for the big 50th birthday party, which is 4 years hence.
Finest regards,
troy and christina
Subscribe to:
Posts (Atom)